Steel band side treating process
A processing technology and edge technology, which is applied in the field of large-scale cold-formed steel production line technology to achieve the effect of reducing investment costs
- Summary
- Abstract
- Description
- Claims
- Application Information
AI Technical Summary
Problems solved by technology
Method used
Image
Examples
Embodiment Construction
[0016] Below, with reference to the accompanying drawings, the embodiment of the steel strip edge processing technology and the device used in the present invention will be described in detail.
[0017] The steel strip edge processing technology and the device used in the present invention are combined with edge disc shears and edge planer, supplemented by edge extrusion molding in the forming process, which solves the problem of high-frequency parallelism of the steel ends to be welded. Degree problem.
[0018] The disc shears in the present invention first cut the edge of the raw material to determine the width, and then the edge is planed out of the groove by the edge planer. Measure the edge bevel to the final welding process angle and end surface quality.
[0019] Referring to Fig. 1 Fig. 2, Fig. 3, wherein, Fig. 1 is the schematic diagram that utilizes disc shearing edge trimming process in the present invention; Fig. 2 is the schematic diagram that utilizes edge planer...
PUM
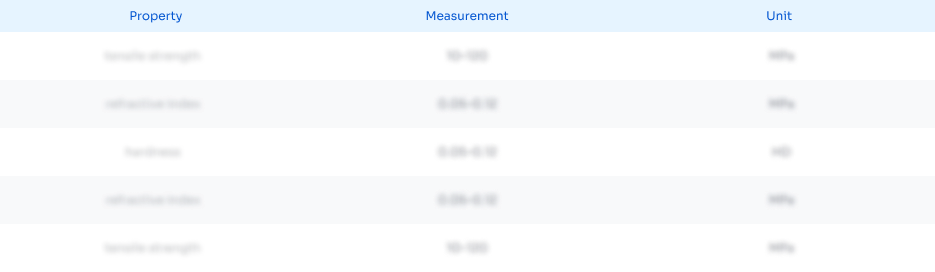
Abstract
Description
Claims
Application Information

- Generate Ideas
- Intellectual Property
- Life Sciences
- Materials
- Tech Scout
- Unparalleled Data Quality
- Higher Quality Content
- 60% Fewer Hallucinations
Browse by: Latest US Patents, China's latest patents, Technical Efficacy Thesaurus, Application Domain, Technology Topic, Popular Technical Reports.
© 2025 PatSnap. All rights reserved.Legal|Privacy policy|Modern Slavery Act Transparency Statement|Sitemap|About US| Contact US: help@patsnap.com