Process for coating aluminium oxide at surface of plastic floor tile
A plastic floor tile and surface coating technology, which is applied to the surface coating liquid device, coating, etc., can solve the problems of easy falling off, inability to form a matte effect, inability to form wear resistance, scratch resistance and anti-slip properties
- Summary
- Abstract
- Description
- Claims
- Application Information
AI Technical Summary
Problems solved by technology
Method used
Image
Examples
Embodiment Construction
[0047] In order to enable readers to have a more detailed and clear understanding of the purpose, efficacy and structural features of the present invention, the preferred embodiments are now listed and detailed in conjunction with the accompanying drawings as follows:
[0048] Please refer to Image 6 , Figure 7 , Figure 7 A. Figure 7 B. Figure 7C , Figure 8 and Figure 9 shown, which are respectively the flow block diagram of the present invention, the manufacturing flow chart of the present invention, the present invention Figure 7 The partially enlarged schematic diagrams of A, B, and C, the cross-sectional schematic diagram and the three-dimensional schematic diagram of the product produced by the method of the present invention can be seen from the diagrams, and the method for coating the surface of the plastic floor tile of the present invention includes the following steps: Plastic floor tile semi-finished products 10 feeding table preparation; photosensitiv...
PUM
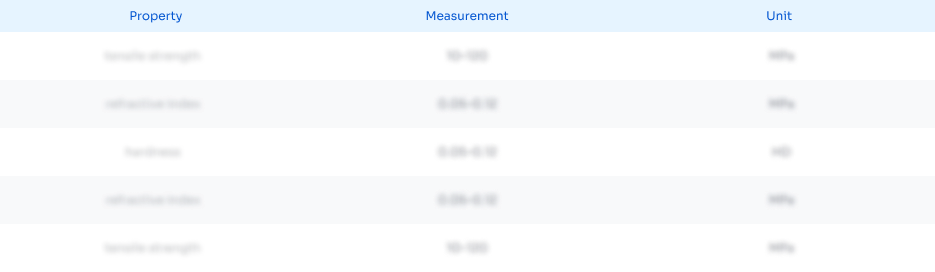
Abstract
Description
Claims
Application Information

- R&D
- Intellectual Property
- Life Sciences
- Materials
- Tech Scout
- Unparalleled Data Quality
- Higher Quality Content
- 60% Fewer Hallucinations
Browse by: Latest US Patents, China's latest patents, Technical Efficacy Thesaurus, Application Domain, Technology Topic, Popular Technical Reports.
© 2025 PatSnap. All rights reserved.Legal|Privacy policy|Modern Slavery Act Transparency Statement|Sitemap|About US| Contact US: help@patsnap.com