Hot-pressing sintering method and mould for ceramic,hard metal products with holes
A cemented carbide, hot-pressing sintering technology, applied in molds, manufacturing tools, ceramic molding machines, etc., can solve the problems of high production cost, low productivity, and reduced product quality, and achieve low production cost, long mold life, and product quality. good quality effect
- Summary
- Abstract
- Description
- Claims
- Application Information
AI Technical Summary
Problems solved by technology
Method used
Image
Examples
Embodiment 2
[0022] This embodiment takes the production of φ16.5×8.5 products as an example:
[0023] Si 3 N 4 The composite powder was cold-pressed into green blanks (blanks 6) with a central aperture of φ16.5×18mm and a central aperture of φ6.0mm, a total of 42 pieces, and each cavity was filled separately, and the blank loading and sintering methods were the same as in Example 1.
[0024] In the mold of this embodiment, the inner and outer diameters and heights of the outer mold cover 1 and the outer diameter and height of the inner mold cover 2 are the same as those in Example 1, and the mold cavity 8 is used in this embodiment. Seven cylindrical holes with a diameter of φ16.65mm The mold cavity, the upper and lower punches 3 and 7 are also seven punches with mandrel holes 4, the diameter of the punch is φ16.5mm, and the height is 50mm; the diameter of the partition 5 is φ16.5mm, and the thickness is 8mm. A total of 49; mandrel hole diameter φ5.4mm; mandrel 4 length 270mm, diamete...
PUM
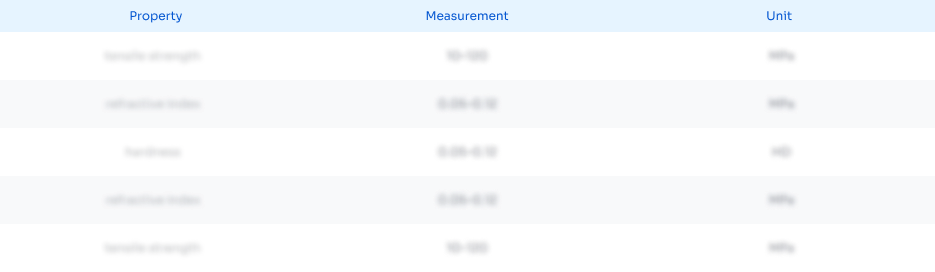
Abstract
Description
Claims
Application Information

- R&D
- Intellectual Property
- Life Sciences
- Materials
- Tech Scout
- Unparalleled Data Quality
- Higher Quality Content
- 60% Fewer Hallucinations
Browse by: Latest US Patents, China's latest patents, Technical Efficacy Thesaurus, Application Domain, Technology Topic, Popular Technical Reports.
© 2025 PatSnap. All rights reserved.Legal|Privacy policy|Modern Slavery Act Transparency Statement|Sitemap|About US| Contact US: help@patsnap.com