Powdery pigment preparations for dyeing films
A kind of pigment preparation and powdery technology, which is applied in the direction of organic dyes, pigment paste, thin material treatment, etc., can solve the problem of not being able to prevent embrittlement spots of the film, and achieve the effect of high pigment concentration
- Summary
- Abstract
- Description
- Claims
- Application Information
AI Technical Summary
Problems solved by technology
Method used
Examples
Embodiment 1
[0034] In a dispersion kneader, 225 parts of acrylate resin (composed of 58 mol% ethyl methacrylate, 39 mol% n-butyl methacrylate and 3 mol% methacrylic acid; molecular weight 59000g / mol) and 9 parts epoxy Soybean oil is mixed at room temperature. Then, introduce steam (130°C) to plasticize the material. Into the plastic material, knead 225 parts of C.I. Pigment Blue 15:1 one by one within 15 minutes, and knead for another 30 minutes at 110°C. Then, the material is crushed under the condition of adding a certain amount of water, the kneader is turned off, and the brittle material is crushed in the kneader after cooling. It is then ground in a mechanical mill. A powdered pigment preparation is formed.
Embodiment 2
[0036] In a dispersion kneader, 225 parts of acrylate resin (composed of 60 mol% ethyl methacrylate, 38 mol% n-butyl methacrylate and 2 mol% methacrylic acid; molecular weight 60000g / mol) and 9 parts epoxy Soybean oil is mixed at room temperature. Then, introduce steam (130°C) to plasticize the material. Into the plastic mass, knead 225 parts of C.I. Pigment Violet 19 in portions within 15 minutes, and knead for another 30 minutes at 110°C. Then, the material is crushed under the condition of adding a certain amount of water, the kneader is turned off, and the brittle material is crushed in the kneader after cooling. It is then ground in a mechanical mill. A powdered pigment preparation is formed.
Embodiment 3
[0038] In a dispersion kneader, 225 parts of acrylate resin (composed of 56 mol% ethyl methacrylate, 40 mol% n-butyl methacrylate and 4 mol% methacrylic acid; molecular weight 60000g / mol) and 9 parts of fatty alcohol The ethoxylates were mixed at room temperature. Then, introduce steam (130°C) to plasticize the material. Into the plastic material, knead 225 parts of C.I. Pigment Red 254 one by one within 20 minutes, and knead for another 30 minutes at 110°C. Then, the material is crushed under the condition of adding a certain amount of water, the kneader is turned off, and the brittle material is crushed in the kneader after cooling. It is then ground in a mechanical mill. A powdered pigment preparation is formed.
PUM
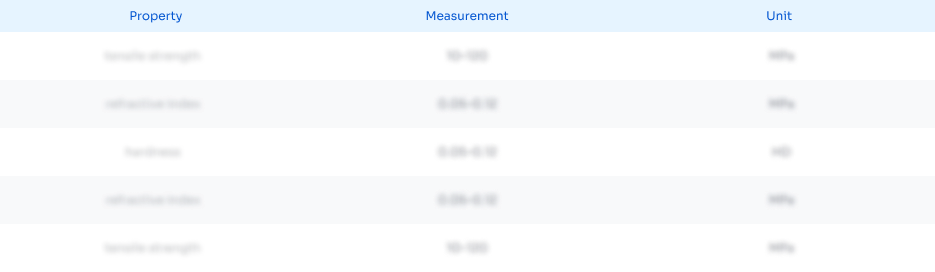
Abstract
Description
Claims
Application Information

- Generate Ideas
- Intellectual Property
- Life Sciences
- Materials
- Tech Scout
- Unparalleled Data Quality
- Higher Quality Content
- 60% Fewer Hallucinations
Browse by: Latest US Patents, China's latest patents, Technical Efficacy Thesaurus, Application Domain, Technology Topic, Popular Technical Reports.
© 2025 PatSnap. All rights reserved.Legal|Privacy policy|Modern Slavery Act Transparency Statement|Sitemap|About US| Contact US: help@patsnap.com