Production of powder cementing agent for glass bat
A powder binder, glass fiber technology, applied in the direction of binder types, ester copolymer binders, non-woven fabrics, etc. Head blockage and other problems, to achieve the effect of low powder moisture content, high solid content, and improved mechanical tensile strength
- Summary
- Abstract
- Description
- Claims
- Application Information
AI Technical Summary
Problems solved by technology
Method used
Examples
Embodiment 1
[0018] 1) Compounding of polymeric emulsifier: In this embodiment, the polymeric (reactive) emulsifier is sodium methacrylate, and the non-ionic emulsifier is OP-8 with an HLB value of 8. Compounding An emulsifier solution is prepared. As shown in Table 1
[0019] Material name
Weight (g)
30
OP-8
10
Deionized water
460
[0020] 2) Configure thermal decomposition initiator: the initiator used in this embodiment is an aqueous solution of potassium persulfate, and the total addition amount is controlled to account for 0.5% of the total reaction monomer content.
[0021] 3) Synthesis of core layer polymer emulsion: Pre-emulsify the reaction monomers as shown in Table 2. Among them, styrene and methyl methacrylate are hard monomers, and isooctyl acrylate is a soft monomer. The weight ratio of the soft and hard monomers is 1:1.5. The pre-emulsified monomer and the initiator solution are gradually added ...
Embodiment 2
[0031] 1) Compounding of polymeric emulsifier: In this example, the polymeric (reactive) emulsifier is sodium methacrylate and the nonionic emulsifier is OP-50 with an HLB value of 18.5. A polymeric emulsifier solution is prepared. As shown in Table 6
[0032] Material name
Weight (g)
Sodium methacrylate
20
OP-50
20
Deionized water
460
[0033] 2) Configuration of thermal decomposition initiator: the initiator used in this embodiment is ammonium persulfate aqueous solution, and the total addition amount is controlled to account for 0.8% of the total reaction monomer content.
[0034] 3) Synthesis of core layer polymer emulsion: Pre-emulsify the reaction monomers as shown in Table 7. Among them, vinyl acetate is the hard monomer, and butyl acrylate is the soft monomer. The weight ratio of soft and hard monomers is 1:1. The pre-emulsified monomer and the initiator solution were gradually added dropwise into a...
PUM
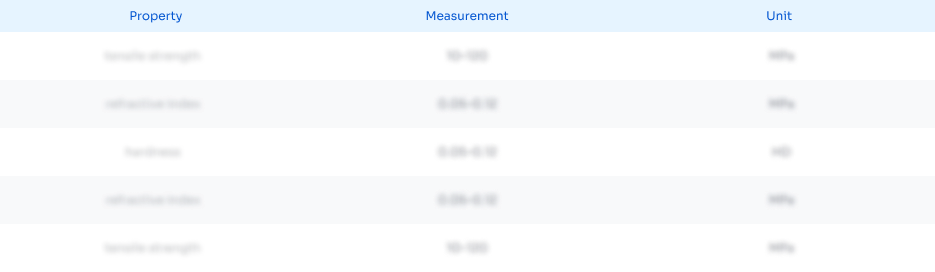
Abstract
Description
Claims
Application Information

- R&D
- Intellectual Property
- Life Sciences
- Materials
- Tech Scout
- Unparalleled Data Quality
- Higher Quality Content
- 60% Fewer Hallucinations
Browse by: Latest US Patents, China's latest patents, Technical Efficacy Thesaurus, Application Domain, Technology Topic, Popular Technical Reports.
© 2025 PatSnap. All rights reserved.Legal|Privacy policy|Modern Slavery Act Transparency Statement|Sitemap|About US| Contact US: help@patsnap.com