Six freedom parallel mechanism for virtual shaft digitally controlled machine tool and measuring machine
A technology of numerically controlled machine tools and virtual axes, applied in the direction of mechanical measuring devices, measuring devices, mechanical devices, etc., can solve problems such as complex manufacturing and assembly, complex structure, and difficult kinematics solutions
- Summary
- Abstract
- Description
- Claims
- Application Information
AI Technical Summary
Problems solved by technology
Method used
Image
Examples
Embodiment Construction
[0014] The technology of the present invention will be further described below by means of accompanying drawings and examples.
[0015] ①, attached figure 1 It is a schematic structural diagram of the six-degree-of-freedom parallel mechanism of the present invention, figure 1 (a) is a three-dimensional stereogram of the parallel mechanism, figure 1 (b) is its two-dimensional plane expansion diagram. It consists of an upper moving platform 0, a lower static platform 1 and three connecting legs with the same structure connecting the upper and lower platforms. Each connecting leg is a hybrid chain, including a five-bar 1, 2, 3, 4, 5 passing through five revolving pairs R 1 , R 7 , R 8 , R 9 , R 2 A planar closed-circuit structure composed of connections and two rotating pairs R composed of components 6, 7, and 8 parallel to each other through axes 10 , R 11 The open-chain structure formed; the member 6 of the open-chain structure and the members 3 and 4 of the planar ...
PUM
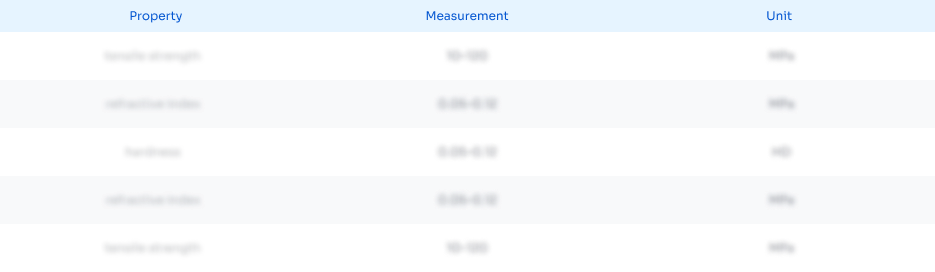
Abstract
Description
Claims
Application Information

- Generate Ideas
- Intellectual Property
- Life Sciences
- Materials
- Tech Scout
- Unparalleled Data Quality
- Higher Quality Content
- 60% Fewer Hallucinations
Browse by: Latest US Patents, China's latest patents, Technical Efficacy Thesaurus, Application Domain, Technology Topic, Popular Technical Reports.
© 2025 PatSnap. All rights reserved.Legal|Privacy policy|Modern Slavery Act Transparency Statement|Sitemap|About US| Contact US: help@patsnap.com