Flexible rotor low speed holographic dynamic balancing method
A technology of flexible rotor and rigid rotor, applied in the field of holographic dynamic balance, to achieve the effect of improving dynamic balancing efficiency, improving balancing accuracy, and reducing the number of times of trial weight lifting
- Summary
- Abstract
- Description
- Claims
- Application Information
AI Technical Summary
Problems solved by technology
Method used
Image
Examples
Embodiment
[0084] Balance scheme 1: Prioritize the balance force component
[0085] The balancing procedure for prioritizing the balancing force components is as follows: Figure 4 As shown, the specific description is as follows:
[0086]1. Measure the basic data. The working speed of the rotor is Ω=3600rpm, and the vibration at the working speed before shutdown is measured; the Bode diagram of the rotor shutdown process is obtained in the experiment, and ω=1900rpm is selected as the balance speed lower than the first-order critical value of the rotor; the measurement test bench is in The vibration in the cranking state is used as the runout, and the shaft vibration value must be deducted from the original runout; measure the original vibration of the rotor when ω=1900rpm (sampling frequency 2kHz, filter 1kHz, sampling points 2048);
[0087] 2. After subtracting the original beating from the vibration data, make a three-dimensional holographic spectrum to obtain the initial phase point...
PUM
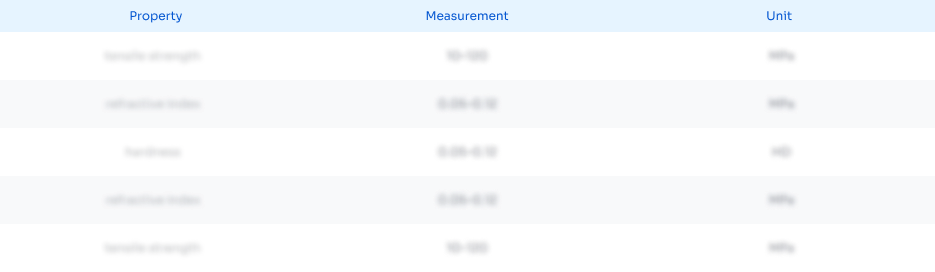
Abstract
Description
Claims
Application Information

- R&D
- Intellectual Property
- Life Sciences
- Materials
- Tech Scout
- Unparalleled Data Quality
- Higher Quality Content
- 60% Fewer Hallucinations
Browse by: Latest US Patents, China's latest patents, Technical Efficacy Thesaurus, Application Domain, Technology Topic, Popular Technical Reports.
© 2025 PatSnap. All rights reserved.Legal|Privacy policy|Modern Slavery Act Transparency Statement|Sitemap|About US| Contact US: help@patsnap.com