Cleaning method of esterifying polycondensation step for polyester preparing equipment and pipeline
An equipment and esterification technology, applied in chemical instruments and methods, cleaning methods using liquids, cleaning methods and utensils, etc., can solve the problems of prolonged driving time, large recycling workload, high heat load, and achieve high safety, Good cleaning effect and low heat load effect
- Summary
- Abstract
- Description
- Claims
- Application Information
AI Technical Summary
Problems solved by technology
Method used
Image
Examples
Embodiment Construction
[0010] The names of equipment and chemical substances are:
[0011] R-21 The first esterification tank R-22 The second esterification tank
[0012] R-31 The first polycondensation tank R-32 The second polycondensation tank
[0013] R-33 The third polycondensation tank T-21 The first rectification tower
[0014] T-22 Second Distillation Column F-22 Melt Filter
[0015] F-33 Melt Filter GP-22 Melt Transfer Pump
[0016] GP-33-1 Melt Transfer Pump EG Glycol
[0017] KOH potassium hydroxide TEG triethylene glycol
[0018] 1. Use 1.0% KOH-EG solution for the first cleaning:
[0019] 1. Cool R-21 to 190°C, introduce 14 tons of EG, start the R-21 agitator to stir, add 140 kg of KOH, control the internal pressure of R-21 to 0.14MPa, gradually increase the temperature to 220°C, and keep the cleaning time for 3 hours. T-21 was cleaned with EG steam in R-21.
[0020] After 2.3 hours, R-21 cools down to 190°C, transfers 7.0 tons of cleaning liquid from R-21 to R-22, turns off the...
PUM
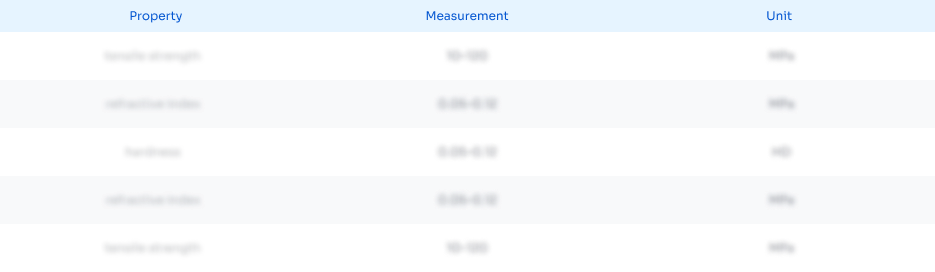
Abstract
Description
Claims
Application Information

- R&D
- Intellectual Property
- Life Sciences
- Materials
- Tech Scout
- Unparalleled Data Quality
- Higher Quality Content
- 60% Fewer Hallucinations
Browse by: Latest US Patents, China's latest patents, Technical Efficacy Thesaurus, Application Domain, Technology Topic, Popular Technical Reports.
© 2025 PatSnap. All rights reserved.Legal|Privacy policy|Modern Slavery Act Transparency Statement|Sitemap|About US| Contact US: help@patsnap.com