Spraying painting material for slide bearing
A technology of spraying materials and sliding bearings, which is applied in the direction of metal material coating process, coating, molten spraying, etc., can solve the problems of unsatisfactory overall use effect, brittle ceramic mounting blocks, accidents, etc., to improve service life, The effect of reducing requirements and reducing the amount of spare parts required
- Summary
- Abstract
- Description
- Claims
- Application Information
AI Technical Summary
Problems solved by technology
Method used
Examples
Embodiment Construction
[0013] The present invention will be discussed in detail below in conjunction with the examples.
[0014] The sliding bearing spraying material of the present invention is Co-Cr-W-Mo self-fluxing alloy, and its composition ratio is as follows in Table 1:
[0015] Chemical composition (weight%)
C
co
Mo
W
Si
B
Cr
Fe
Example 1
0.1
56.9
10.5
6.0
1.0
4.5
20.0
1.0
Example 2
0.15
42.0
12.0
8.0
3.5
2.5
22.0
9.85
Example 3
0.2
29.8
14.0
12.0
5.0
1.0
25.0
13.0
[0016] The spraying equipment adopts oxyacetylene flame spray gun, and completes the processing process of the relative sliding surface coating of the inner and outer sleeves of the sliding bearing through preheating-spraying-tempering-turning-grinding. The technical parameters of the obtained coating are s...
PUM
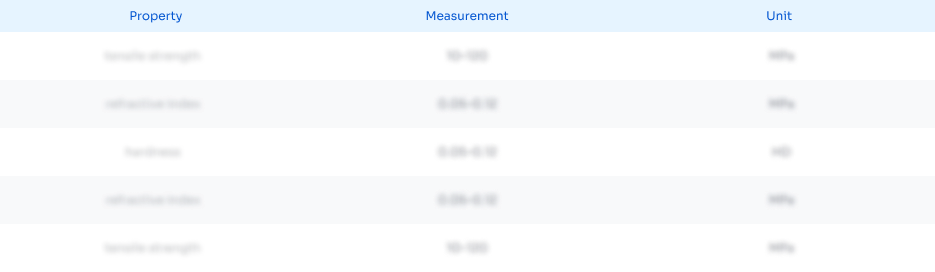
Abstract
Description
Claims
Application Information

- R&D
- Intellectual Property
- Life Sciences
- Materials
- Tech Scout
- Unparalleled Data Quality
- Higher Quality Content
- 60% Fewer Hallucinations
Browse by: Latest US Patents, China's latest patents, Technical Efficacy Thesaurus, Application Domain, Technology Topic, Popular Technical Reports.
© 2025 PatSnap. All rights reserved.Legal|Privacy policy|Modern Slavery Act Transparency Statement|Sitemap|About US| Contact US: help@patsnap.com