Arrangement method of copper plate strip hot rolling workshop and hot rolling process
A layout method and workshop technology, applied in the direction of manufacturing tools, metal rolling, metal rolling, etc., can solve the difficulty in meeting the differentiated requirements of face milling and online solid solution coiling quality, poor flexibility of production process, and production auxiliary time Long and other issues, to achieve the effect of improving site utilization coefficient, perfect configuration, and diverse functions
- Summary
- Abstract
- Description
- Claims
- Application Information
AI Technical Summary
Problems solved by technology
Method used
Image
Examples
Embodiment Construction
[0028] The technical solutions in the embodiments of the present invention will be clearly and completely described below with reference to the accompanying drawings in the embodiments of the present invention. Obviously, the described embodiments are only a part of the embodiments of the present invention, but not all of the embodiments. Based on the embodiments of the present invention, all other embodiments obtained by those of ordinary skill in the art without creative efforts shall fall within the protection scope of the present invention.
[0029] see figure 2 , the present invention provides a kind of technical scheme:
[0030] A method for arranging a hot rolling workshop for copper strips, comprising a two-roll reversible hot rolling mill 1, a walking ingot heating furnace 2, a double-sided milling machine 3, a hot rolling mill drive system 6, a water spray cooling system 7, a thermal Rolling coiler 8, outgoing roller table 9, double-cone head uncoiler 10, post-mill...
PUM
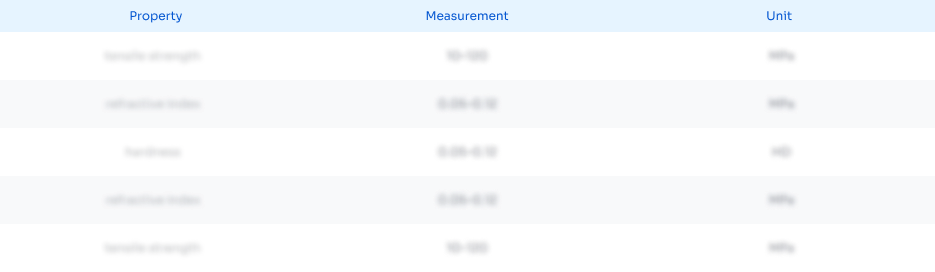
Abstract
Description
Claims
Application Information

- R&D
- Intellectual Property
- Life Sciences
- Materials
- Tech Scout
- Unparalleled Data Quality
- Higher Quality Content
- 60% Fewer Hallucinations
Browse by: Latest US Patents, China's latest patents, Technical Efficacy Thesaurus, Application Domain, Technology Topic, Popular Technical Reports.
© 2025 PatSnap. All rights reserved.Legal|Privacy policy|Modern Slavery Act Transparency Statement|Sitemap|About US| Contact US: help@patsnap.com