Feed-forward control method, feed-forward industrial personal computer and feed-forward control system for sliding steerable drilling
A sliding-steering and feed-forward control technology, which is applied in the automatic control system of drilling, directional drilling, drilling equipment, etc., can solve the problems of high drilling operation risk, prone to trajectory deviation, and hysteresis of drilling control quantity, so as to reduce the cost. and operation risks, improve the accuracy of automatic control, and avoid the effect of time-consuming control
- Summary
- Abstract
- Description
- Claims
- Application Information
AI Technical Summary
Problems solved by technology
Method used
Image
Examples
Embodiment Construction
[0069] The technical solutions in the embodiments herein will be clearly and completely described below with reference to the accompanying drawings in the embodiments herein. Obviously, the described embodiments are only a part of the embodiments herein, rather than all the embodiments. Based on the embodiments herein, all other embodiments obtained by persons of ordinary skill in the art without creative efforts shall fall within the scope of protection herein.
[0070] It should be noted that the terms "first", "second" and the like in the description and claims herein and the above drawings are used to distinguish similar objects, and are not necessarily used to describe a specific sequence or sequence. It is to be understood that data so used may be interchanged under appropriate circumstances such that the embodiments herein described can be practiced in sequences other than those illustrated or described herein. Furthermore, the terms "comprising" and "having", and any v...
PUM
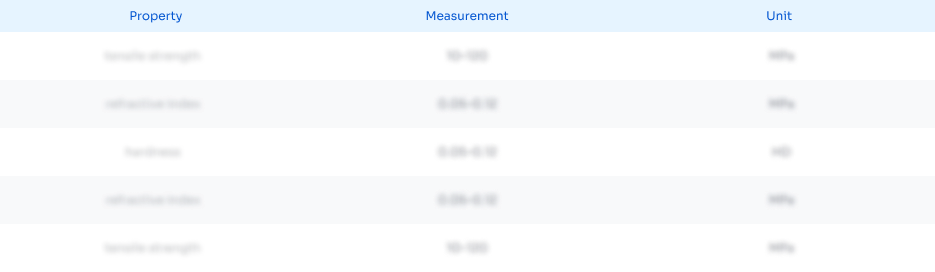
Abstract
Description
Claims
Application Information

- Generate Ideas
- Intellectual Property
- Life Sciences
- Materials
- Tech Scout
- Unparalleled Data Quality
- Higher Quality Content
- 60% Fewer Hallucinations
Browse by: Latest US Patents, China's latest patents, Technical Efficacy Thesaurus, Application Domain, Technology Topic, Popular Technical Reports.
© 2025 PatSnap. All rights reserved.Legal|Privacy policy|Modern Slavery Act Transparency Statement|Sitemap|About US| Contact US: help@patsnap.com