Straight spur gear finite element mesh automatic generation method based on tooth profile and computer equipment
A spur gear, automatic generation technology, applied in design optimization/simulation, geometric CAD and other directions, can solve the problems of low work efficiency and low grid node accuracy, and achieve the effect of improving efficiency and low computational complexity
- Summary
- Abstract
- Description
- Claims
- Application Information
AI Technical Summary
Problems solved by technology
Method used
Image
Examples
Embodiment approach 1
[0096] Embodiment 1. A method for automatically generating finite element meshes of spur gears based on tooth profile, the method comprising:
[0097] Step 1. Take the symmetry axis of a gear tooth section in the spur gear as the y-axis, and take the straight line passing through the center of the gear circle and perpendicular to the y-axis as the x-axis to establish a Cartesian coordinate system;
[0098] Step 2. Under the Cartesian coordinate system, obtain the tooth profile of half a gear tooth, and the tooth profile takes the intersection of the tooth profile and the tip circle as the starting point, and takes the tooth root profile point as the end point;
[0099] Step 3. According to the tooth profile, the inner circle radius of the gear and the boundary line of the gear teeth, establish a half gear tooth frame;
[0100] Step 4. Divide the half gear tooth frame into an upper area, a middle area and a lower area, wherein the upper area corresponds to the gear teeth part, ...
Embodiment approach 2
[0109] Embodiment 2, this embodiment is a further limitation of the method for automatically generating finite element meshes of spur gears based on tooth profile described in Embodiment 1. In this embodiment, the step 4 is done. Further limited, specifically including:
[0110] Step 4.1. Obtain the difference between the ordinates of the starting point and the ending point;
[0111] Step 4.2, set a preset ratio, and determine the difference between the ordinate of the boundary line and the ordinate of the end point according to the difference between the ordinates and the opportunity of the preset ratio;
[0112] Step 4.3, according to the difference between the ordinate of the boundary line and the ordinate of the end point, obtain the boundary line of the half-gear frame at the upper and lower azimuths of the end point;
[0113] Step 4.4, according to the boundary line, divide the half-gear frame into an upper area, a middle area and a lower area.
[0114] In this embodim...
Embodiment approach 3
[0115] Embodiment 3, this embodiment is a further limitation of the method for automatically generating finite element meshes of spur gears based on tooth profile described in Embodiment 1. In this embodiment, the step 5 is done. Further limited, specifically including:
[0116] Step 5.1, for the upper area, set the upper vertical fraction parameter and the upper horizontal fraction parameter, and perform grid division on the upper area according to the upper vertical fraction parameter and the upper horizontal fraction parameter to obtain the upper All nodes in the area, all the nodes in the upper area include nodes on the boundary line between the upper area and the middle area;
[0117] Step 5.2, for the middle area, set the middle vertical share parameter, according to the middle vertical share parameter, the upper horizontal share parameter and the node on the boundary line between the upper area and the middle area, and Use quadratic Bezier curve to mesh the middle regi...
PUM
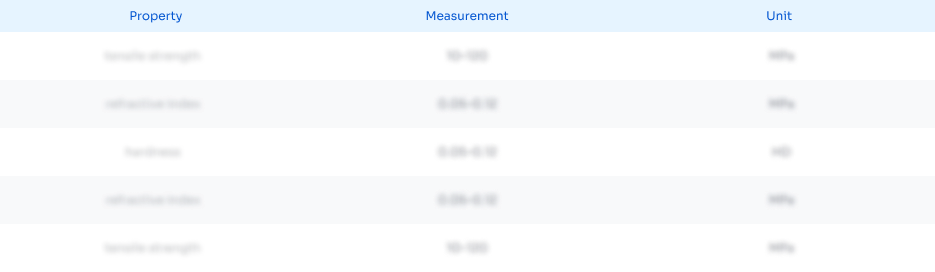
Abstract
Description
Claims
Application Information

- Generate Ideas
- Intellectual Property
- Life Sciences
- Materials
- Tech Scout
- Unparalleled Data Quality
- Higher Quality Content
- 60% Fewer Hallucinations
Browse by: Latest US Patents, China's latest patents, Technical Efficacy Thesaurus, Application Domain, Technology Topic, Popular Technical Reports.
© 2025 PatSnap. All rights reserved.Legal|Privacy policy|Modern Slavery Act Transparency Statement|Sitemap|About US| Contact US: help@patsnap.com