Textile wastewater treatment agent and preparation method thereof
A textile wastewater and treatment agent technology, which is applied in textile industry wastewater treatment, energy wastewater treatment, water/sewage treatment, etc., can solve problems such as high content of organic matter and harmful substances, complex composition of textile wastewater, water body hazards, etc., to achieve strong Adsorption capacity, improvement of decolorization rate and COD removal rate, improvement of viscosity
- Summary
- Abstract
- Description
- Claims
- Application Information
AI Technical Summary
Problems solved by technology
Method used
Image
Examples
Embodiment 1
[0034] A preparation method of a textile wastewater treatment agent, comprising the following steps:
[0035] (a) each component is weighed according to the proportion by weight described in the formula, and 50 parts of modified red mud, 10 parts of diatomite and 8 parts of activated carbon are reacted at 60° C. and 400 r / min for 2 h, and then cooled for later use;
[0036] (b) subsequently adding 30 parts of flocculant, 8 parts of boric acid and 27 parts of modified starch into the product obtained in step (a), adding it into the mixer, controlling the temperature to be 50°C, stirring for 30min, and obtaining a wastewater treatment agent after the stirring.
[0037] Wherein, the preparation method of described modified red mud comprises the following steps:
[0038] (1) 20 parts of red mud are pulverized and then sieved, and the impurities of crushed ore chips are removed to obtain the red mud with impurity removal, then the red mud is added to 200 parts of 10% hydrogen perox...
Embodiment 2
[0043] A preparation method of a textile wastewater treatment agent, comprising the following steps:
[0044] (a) each component is weighed according to the proportion by weight described in the formula, and 40 parts of modified red mud, 7 parts of diatomite and 10 parts of activated carbon are reacted at 50° C. and 300 r / min for 3 h, and then cooled for later use;
[0045] (b) subsequently adding 20 parts of flocculant, 10 parts of boric acid and 20 parts of modified starch, adding the product obtained in step (a), adding it into the mixer, controlling the temperature to be 40°C, stirring for 60min, and obtaining a wastewater treatment agent after stirring.
[0046] Wherein, the preparation method of described modified red mud comprises the following steps:
[0047] (1) 15 parts of red mud are pulverized and then sieved, and the impurities of crushed ore chips are removed to obtain the red mud with impurity removal, then the red mud is added to 200 parts of 5% hydrogen peroxi...
Embodiment 3
[0052] A preparation method of a textile wastewater treatment agent, comprising the following steps:
[0053] (a) each component is weighed according to the proportion by weight described in the formula, and 45 parts of modified red mud, 10 parts of diatomite and 10 parts of activated carbon are reacted at 55° C. and 400 r / min for 3 h, and are used after cooling;
[0054] (b) subsequently adding 25 parts of flocculant, 7 parts of boric acid and 23 parts of modified starch, adding the product obtained in step (a), adding into the mixer, controlling the temperature to be 45°C, stirring for 50min, and obtaining a waste water treatment agent after stirring.
[0055] Wherein, the preparation method of described modified red mud comprises the following steps:
[0056] (1) 20 parts of red mud are pulverized and then sieved, and the impurities of crushed ore chips are removed to obtain the red mud with impurity removal, then the red mud is added to 200 parts of 7% hydrogen peroxide an...
PUM
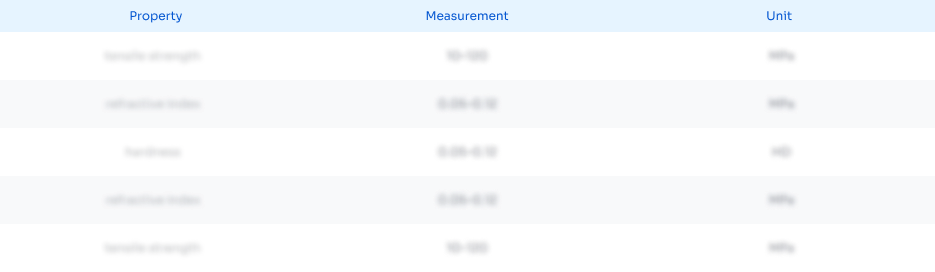
Abstract
Description
Claims
Application Information

- Generate Ideas
- Intellectual Property
- Life Sciences
- Materials
- Tech Scout
- Unparalleled Data Quality
- Higher Quality Content
- 60% Fewer Hallucinations
Browse by: Latest US Patents, China's latest patents, Technical Efficacy Thesaurus, Application Domain, Technology Topic, Popular Technical Reports.
© 2025 PatSnap. All rights reserved.Legal|Privacy policy|Modern Slavery Act Transparency Statement|Sitemap|About US| Contact US: help@patsnap.com