Preheating type side heating gas hot galvanizing furnace
A hot-dip galvanizing and heating furnace technology, which is applied in hot-dip galvanizing process, coating, metal material coating process, etc., can solve the problems of dust residue, low heating efficiency, difficult covering position of hot-dip galvanizing furnace, etc., and achieve replacement The effect of simplification and improving the quality of galvanized finished products
- Summary
- Abstract
- Description
- Claims
- Application Information
AI Technical Summary
Problems solved by technology
Method used
Image
Examples
Embodiment 1
[0042] like Figure 1-8 As shown, the present invention provides a preheating type side heating gas hot-dip galvanizing furnace, including a galvanizing furnace 1, a heating mechanism 2 is provided on the side of the galvanizing furnace 1, and a lifting mechanism 3 is provided on the top of the galvanizing furnace 1, The lifting mechanism 3 includes a holding box 33, and a vibration mechanism 34 is arranged inside the holding box 33. The vibration mechanism 34 includes a groove 344. The inner wall of the groove 344 is fixedly connected to the front of the third motor 346, and the output end of the third motor 346 is fixed. A No. 1 rotating rod 345 is connected. The surface of the No. 1 rotating rod 345 is fixedly connected with a rotating disk 342. The front side of 345 is movably connected with the back side of the inner wall of groove 344 .
[0043]In this embodiment, when the No. 3 motor 346 is activated, the No. 3 motor 346 will drive the No. 1 rotating rod 345 to rotate....
Embodiment 2
[0045] like Figure 1-8 As shown, on the basis of Embodiment 1, the present invention provides a technical solution: preferably, the heating mechanism 2 includes a filter mechanism 24, the filter mechanism 24 includes a filter pipe 243, and the side of the filter pipe 243 is overlapped with a heating shell 23, The inside of the heating shell 23 is provided with a placement slot, the side of the filter pipe 243 is fixedly connected to the inside of the placement slot with a clamping plate 242, the side of the inner wall of the placement slot is movably connected with a connecting plate 244, and the bottom of the heating shell 23 is fixedly connected with a fixed shell 247, the No. 4 motor 248 is fixedly connected to the front of the inner wall of the fixed housing 247, and the output end of the No. 4 motor 248 is fixedly connected to a harness rod 246, the front of the harness rod 246 extends to the outside of 2477, and the surface of the harness rod 246 is A connecting rope 24...
Embodiment 3
[0048] like Figure 1-8 As shown, on the basis of Embodiment 1, the present invention provides a technical solution: preferably, the galvanizing furnace 1 includes a stirring and cutting mechanism 12, and the stirring and cutting mechanism 12 includes a fixing block 122, and the surface of the fixing block 122 is fixedly connected with cutting The ring piece 121, the bottom of the cutting ring piece 121 is fixedly connected with the second rotating rod 123, the surface of the second rotating rod 123 is fixedly connected with an auger 124, and the surface of the auger 124 is fixedly connected with a cutting blade 125.
[0049] In this embodiment, when the No. 2 rotating rod 123 rotates, the rotation of the No. 2 rotating rod 123 directly drives the fixed block 122 to continue to rotate, and then drives the cutting ring 121 to cut the zinc block. The rotation will also drive the rotation of the auger 124. The rotation of the auger 124 will cut the zinc block through the cutting ...
PUM
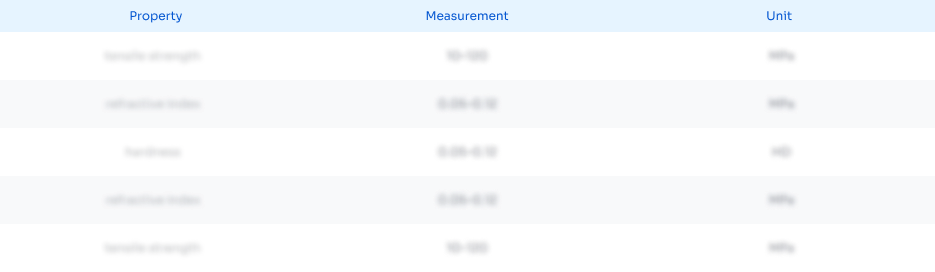
Abstract
Description
Claims
Application Information

- Generate Ideas
- Intellectual Property
- Life Sciences
- Materials
- Tech Scout
- Unparalleled Data Quality
- Higher Quality Content
- 60% Fewer Hallucinations
Browse by: Latest US Patents, China's latest patents, Technical Efficacy Thesaurus, Application Domain, Technology Topic, Popular Technical Reports.
© 2025 PatSnap. All rights reserved.Legal|Privacy policy|Modern Slavery Act Transparency Statement|Sitemap|About US| Contact US: help@patsnap.com