Calcium-manganese-oxygen thermoelectric material and preparation method thereof
A technology of calcium-manganese-oxygen thermoelectric and thermoelectric materials, which is applied in the direction of lead-out wire materials of thermoelectric devices, manufacture/processing of thermoelectric devices, etc., can solve the problem of high Seebeck coefficient and thermal conductivity, low thermoelectric conversion efficiency and difficult Industrial quantitative production and other issues, to achieve the effect of improving Seebeck coefficient, optimizing thermoelectric conversion efficiency, and reducing thermal conductivity
- Summary
- Abstract
- Description
- Claims
- Application Information
AI Technical Summary
Problems solved by technology
Method used
Image
Examples
Embodiment 1
[0026] Embodiment 1, a kind of calcium manganese oxygen thermoelectric material, with cubic phase CaMnO 3 As the matrix phase, lamellar CaO is used as the intercalation phase, and the intercalation phase is dispersed and arranged in the matrix phase to form a tetragonal perovskite intergrowth structure CaO (CaMnO 3 ) m , where m=1, 2, 3... 15 -10^ 19 / cm^ 3 , so as to improve the Seebeck coefficient of the thermoelectric material, so as to further optimize the thermoelectric conversion efficiency of the thermoelectric material.
[0027] Further, the tetragonal perovskite intergrowth structure CaO (CaMnO 3 ) m Where m=2-10, m is a natural number. In the preferred structure, a sharper CaMnO can be formed 3 -CaO layered structure. Cubic CaMnO 3 The chimeric relationship with the intercalation phase CaO generates a Ruddlesden-Popper structure, which can increase the complexity of the structure, increase phonon diffraction, and reduce thermal conductivity. Specifically, i...
Embodiment 2
[0031] Embodiment 2, a preparation method of calcium manganese oxygen thermoelectric material, comprising the following steps:
[0032] S1, take CaO and MnO 2 Homogeneous mix, CaO and MnO 2 The ratio of the amount of substances is m+1:m, m=1, 2, 3...∞, and then high-temperature sintering is performed, the sintering temperature is 1200-1600 ° C, and the high-temperature sintering time is 4-18h;
[0033] S2. Ball milling the mixture sintered at high temperature to form powder, wherein the mass ratio of the ball to the mixture is 10-30:1, and the ball milling time is 0.5-4h, so that the particle size of the powder particles reaches 30-1000nm; further , the mass ratio of the ball to the mixture is preferably 15-25:1; further, the particle size of the powder particles formed is preferably 50-800 nm; further, the ball milling time is preferably 0.5-4h. In the present invention, the ball milling step is the basis for reducing the hot pressing process conditions. Therefore, when bal...
Embodiment 2-1
[0036] Example 2-1, take 22.533g of lamellar CaO and 17.4667g of MnO 2 Mix uniformly, then carry out high temperature sintering, the sintering temperature is 1200 ° C, and sintering for 4 hours; the high temperature sintered mixture is ball-milled to form powder, wherein the mass ratio of the ball to the mixture is 10:1. Until the particle size of the powder particles is 30-1000nm, the ball milling time is 0.5h; the powder is collected, and the powder is hot-pressed with a hot-pressing die under argon gas at a pressure of 40MPa, a temperature of 600°C, and a heating rate of 8°C / min. , the holding time is 15min, and the tetragonal perovskite intergrowth structure Ca is obtained. 2 MnO 4 Thermoelectric materials, quality inspection of thermoelectric materials, XRD calculation of materials before ball milling and finished samples (that is, samples after ball milling), quality inspection results are shown in figure 2 , Image 6 , Figure 7 , it can be seen from the test resul...
PUM
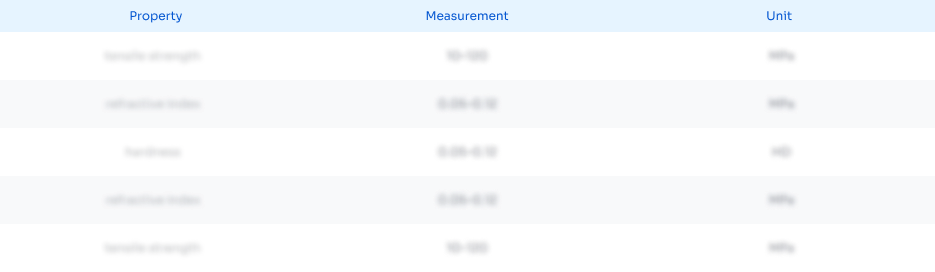
Abstract
Description
Claims
Application Information

- Generate Ideas
- Intellectual Property
- Life Sciences
- Materials
- Tech Scout
- Unparalleled Data Quality
- Higher Quality Content
- 60% Fewer Hallucinations
Browse by: Latest US Patents, China's latest patents, Technical Efficacy Thesaurus, Application Domain, Technology Topic, Popular Technical Reports.
© 2025 PatSnap. All rights reserved.Legal|Privacy policy|Modern Slavery Act Transparency Statement|Sitemap|About US| Contact US: help@patsnap.com