Redundancy control method for flame cutting system of continuous casting machine
A flame cutting and redundant control technology, applied in the field of steel continuous casting, can solve problems such as maintenance difficulties, frequent cutting machine limit failures, and restrictions on equipment operation stability and continuity, so as to solve potential safety hazards and ensure stability Effect
- Summary
- Abstract
- Description
- Claims
- Application Information
AI Technical Summary
Problems solved by technology
Method used
Examples
Embodiment Construction
[0013] The following are specific embodiments of the present invention to further describe the technical solutions of the present invention, but the protection scope of the present invention is not limited to these embodiments. All changes or equivalent substitutions that do not depart from the concept of the present invention are included in the protection scope of the present invention.
[0014] A redundant control method for a flame cutting system of a continuous casting machine, the steps are as follows:
[0015] 1) The control program of the continuous casting flame cutting system is combed in detail, and the electrical limit points involved in each flow are counted from the original control program to form a list;
[0016] 2) Design the corresponding analog limit according to the characteristics of each electrical limit and the principle of program control;
[0017] 3) Corresponding to the list of statistics in step 1), the analog limit designed in step 2) and the corre...
PUM
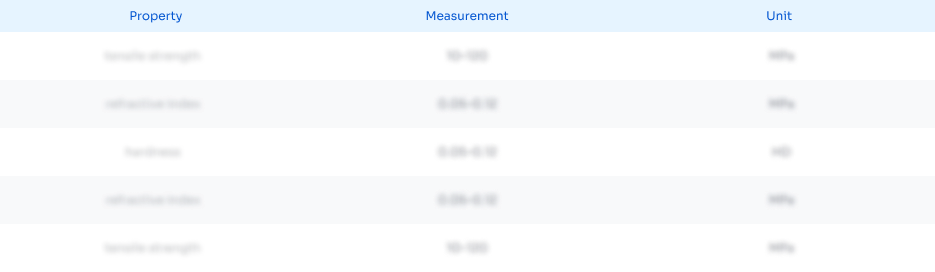
Abstract
Description
Claims
Application Information

- Generate Ideas
- Intellectual Property
- Life Sciences
- Materials
- Tech Scout
- Unparalleled Data Quality
- Higher Quality Content
- 60% Fewer Hallucinations
Browse by: Latest US Patents, China's latest patents, Technical Efficacy Thesaurus, Application Domain, Technology Topic, Popular Technical Reports.
© 2025 PatSnap. All rights reserved.Legal|Privacy policy|Modern Slavery Act Transparency Statement|Sitemap|About US| Contact US: help@patsnap.com