Radio frequency and direct current co-sputtering gray decorative film layer and method and application thereof
A technology of DC sputtering and RF sputtering, which is applied in the field of coated decorative film products, radio frequency and DC co-sputtering gray decorative film, to achieve the effect of simple process control, process safety, and easy color control
- Summary
- Abstract
- Description
- Claims
- Application Information
AI Technical Summary
Problems solved by technology
Method used
Image
Examples
Embodiment 1
[0034] 1. Use the ABS base material test plate that has been electroplated with copper, nickel and chromium on the surface and brushed. After the surface is cleaned, it is placed on the turntable in the cavity of the coating machine. The RF sputtering power supply is connected to the graphite target, and the DC sputtering power supply is connected to the zirconium target. ;
[0035] 2. Turn on the vacuum pumping system and pump the vacuum in the cavity to 8.0*10 -3 Pa;
[0036] 3. Introduce argon gas to maintain the vacuum degree in the cavity at 4.6*10 -1 Pa, turn on the DC sputtering power supply, adjust the output power of the zirconium target to 100w, and deposit metal Zr for 5min as the bottom layer;
[0037] 4. Introduce argon gas to maintain the vacuum degree in the cavity at 4.6*10 -1 Pa, turn on the RF sputtering power supply and the DC sputtering power supply at the same time, adjust the output power of the RF sputtering power supply to 100w, adjust the output pow...
Embodiment 2
[0041] 1. Use the ABS base material test plate that has been electroplated with copper, nickel and chromium on the surface and brushed. After the surface is cleaned, it is placed on the turntable in the cavity of the coating machine. The RF sputtering power supply is connected to the graphite target, and the DC sputtering power supply is connected to the zirconium target. ;
[0042] 2. Turn on the vacuum pumping system and pump the vacuum in the cavity to 5.0*10 -3 Pa;
[0043] 3. Introduce argon gas to maintain the vacuum degree in the cavity at 4.0*10 -1 Pa, turn on the DC sputtering power supply, adjust the output power of the zirconium target to 50w, and deposit metal Zr for 5min as a primer;
[0044] 4. Introduce argon gas to maintain the vacuum degree in the cavity at 4.0*10 -1 Pa, turn on the RF sputtering power supply and the DC sputtering power supply at the same time, adjust the output power of the RF sputtering power supply to 100w, adjust the output power of the...
Embodiment 3
[0048] 1. Adopt the ABS base material cylindrical piece that has been electroplated with copper, nickel and chromium on the surface and brushed. After the surface is cleaned, it is placed on the turntable in the cavity of the coating machine. The RF sputtering power supply is connected to the graphite target, and the DC sputtering power supply is connected to the zirconium. target;
[0049] 2. Turn on the vacuum pumping system and pump the vacuum in the cavity to 1.0*10 -2 Pa;
[0050] 3. Introduce argon gas to maintain the vacuum degree in the cavity at 6.0*10 -1 Pa, turn on the DC sputtering power supply, adjust the output power of the zirconium target to 100w, and deposit metal Zr for 10min as a primer;
[0051] 4. Introduce argon gas to maintain the vacuum degree in the cavity at 6.0*10 -1 Pa, turn on the RF sputtering power supply and the DC sputtering power supply at the same time, adjust the output power of the RF sputtering power supply to 150w, adjust the output po...
PUM
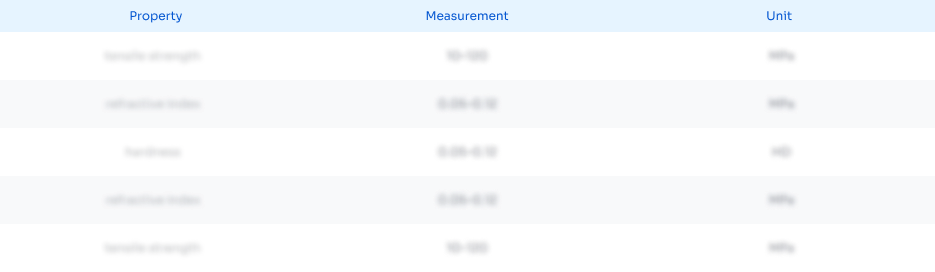
Abstract
Description
Claims
Application Information

- R&D Engineer
- R&D Manager
- IP Professional
- Industry Leading Data Capabilities
- Powerful AI technology
- Patent DNA Extraction
Browse by: Latest US Patents, China's latest patents, Technical Efficacy Thesaurus, Application Domain, Technology Topic, Popular Technical Reports.
© 2024 PatSnap. All rights reserved.Legal|Privacy policy|Modern Slavery Act Transparency Statement|Sitemap|About US| Contact US: help@patsnap.com