Drill floor pipe grabbing manipulator with self-adaptive size
An adaptive and manipulator technology, which is applied in the direction of manipulators, program control manipulators, manufacturing tools, etc., can solve the problems of small opening and closing of fingers and affect the efficiency of automatic pipe arrangement, and achieve the effect of small flight attendant, compact structure and large opening and closing.
- Summary
- Abstract
- Description
- Claims
- Application Information
AI Technical Summary
Problems solved by technology
Method used
Image
Examples
Embodiment 1
[0037] Such as Figure 1-8 As shown, a size-adaptive drill floor pipe grasping manipulator includes a base 1, and a compound gear train reducer 4 is arranged inside the base 1, and the compound gear train reducer 4 drives two output outer shafts 412 and output inner shafts with opposite directions of rotation. Shaft 414, the top of the base 1 is connected with the top cover 2, the two sides of the base 1 are provided with a clamping mechanism, the middle part of the clamping mechanism on one side is hinged with the top cover 2 through a connecting rod, and the connecting rods at the tail ends of the clamping mechanism on both sides are respectively connected with two An output outer shaft 412 and an output inner shaft 414 of opposite rotation are connected. The output mechanism is connected with the composite gear train reducer 4, and the composite gear train reducer 4 drives the output outer shaft 412 and the output inner shaft 414 to rotate in opposite directions. In the cl...
Embodiment 2
[0049] Further illustrate in conjunction with embodiment 1, as Figure 1-8 As shown, a size-adaptive drill floor pipe grasping manipulator of the present invention includes a base 1, a top cover 2, a clamping mechanism 3 (a-b), a compound gear train reducer 4; the compound gear train reducer includes a planetary gear transmission mechanism, Cycloid planetary reduction mechanism, harmonic gear reduction mechanism.
[0050] Among them, the clamping mechanism includes fingers 301 (a-b) and 302 (a-b), connecting rods 303 (a-b), 304 (a-b), rollers 305 (a-b), and roller shafts 308 (a-b); four fingers in pairs, Among them, 301a and 302a are a group, and 301b and 302b are a group, which are respectively installed on both sides of the base 1 and the top cover 2; the upper right finger 301a passes through the upper right tail connecting rod 303a and the output of the compound gear train reducer 4 The inner shaft 414 is connected, and the finger 301a is connected to the top cover 2 by u...
PUM
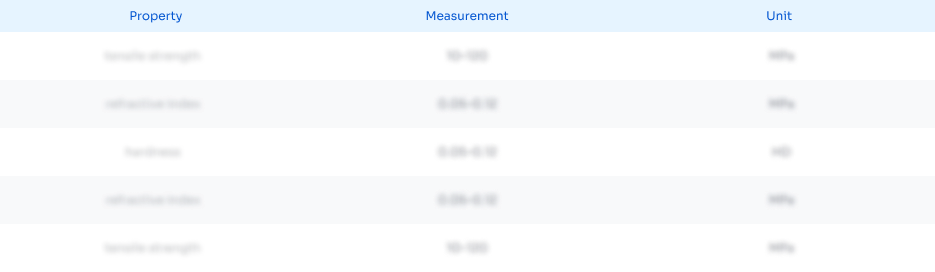
Abstract
Description
Claims
Application Information

- R&D Engineer
- R&D Manager
- IP Professional
- Industry Leading Data Capabilities
- Powerful AI technology
- Patent DNA Extraction
Browse by: Latest US Patents, China's latest patents, Technical Efficacy Thesaurus, Application Domain, Technology Topic, Popular Technical Reports.
© 2024 PatSnap. All rights reserved.Legal|Privacy policy|Modern Slavery Act Transparency Statement|Sitemap|About US| Contact US: help@patsnap.com