Mechanical multi-turn encoder for joint of foot-type robot
A robot joint and encoder technology, applied in metal processing equipment, metal processing, manufacturing tools, etc., can solve the problems of reducing the cost and volume of the encoder, reducing the volume and cost of the encoder, and difficult installation
- Summary
- Abstract
- Description
- Claims
- Application Information
AI Technical Summary
Problems solved by technology
Method used
Image
Examples
Embodiment Construction
[0020] The technical means adopted by the present invention to achieve the intended invention purpose are further described below in conjunction with the drawings and preferred embodiments of the present invention.
[0021] Please refer to figure 1 as shown, figure 1 It is a schematic diagram of the gears of the mechanical multi-turn encoder of the present invention. This mechanical multi-turn encoder comprises driving gear 2, master magnet 3, driven gear 4, slave magnet 5, master magnetic induction chip and slave magnetic induction chip (main magnetic induction chip and slave magnetic induction chip are not in figure 1 shown in ). Wherein, the driving gear 2 is coaxially connected with the motor shaft, and the main magnet 3 is installed on the motor shaft end, coaxially arranged with the driving gear 2, and the driving gear 2 and the main magnet 3 rotate together with the motor shaft. The driven gear 4 is installed on the motor rear end cover 1, the slave magnet 5 is coaxi...
PUM
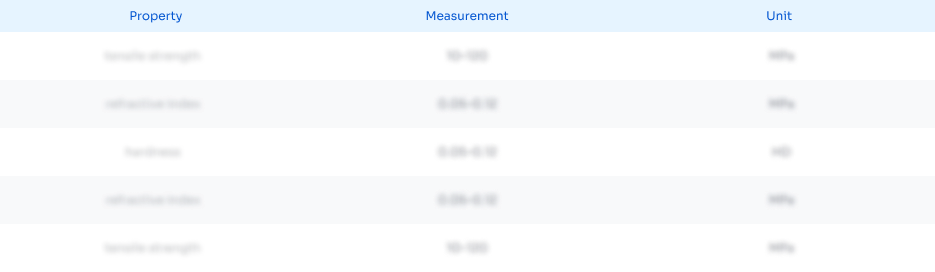
Abstract
Description
Claims
Application Information

- R&D Engineer
- R&D Manager
- IP Professional
- Industry Leading Data Capabilities
- Powerful AI technology
- Patent DNA Extraction
Browse by: Latest US Patents, China's latest patents, Technical Efficacy Thesaurus, Application Domain, Technology Topic, Popular Technical Reports.
© 2024 PatSnap. All rights reserved.Legal|Privacy policy|Modern Slavery Act Transparency Statement|Sitemap|About US| Contact US: help@patsnap.com