Method and device for fixing thermocouple in steel-plate-encased concrete composite member
A technology of composite components and outsourcing steel plates, which is applied in the direction of using electrical devices, measuring devices, and thermometers using electric/magnetic elements that are directly sensitive to heat, can solve the problem that the accuracy of the measuring point position cannot be guaranteed and the occurrence of thermocouple disturbances Offset, thermocouples are vulnerable to impact, etc., to achieve the effect of optimizing the construction sequence, ensuring accurate positioning, and easy operation
- Summary
- Abstract
- Description
- Claims
- Application Information
AI Technical Summary
Problems solved by technology
Method used
Image
Examples
Embodiment 1
[0052] The cross-section of the vertical composite member used in this embodiment is rectangular, and the drilling position and the drilling of the outer cladding steel plate of the experimental member are determined according to the temperature field measurement position, and the position and quantity of the thermocouple measuring points along the thickness direction are determined according to the measurement needs;
[0053] Arrange the thermocouples and bind them into a thermocouple bundle. The cross section of the thermocouple bundle is as follows: Figure 3a As shown, measure the distance from the measuring point to the outer surface of the drilled steel plate on the thermocouple and mark it;
[0054] Weld the fixing bracket on the outer surface of the experimental component;
[0055] First pour the concrete under the drilled hole and vibrate it compactly, and make the upper surface of the concrete flush with the lowest point of the drilled hole;
[0056] Extend the ther...
Embodiment 2
[0059] The cross-section of the vertical composite member used in this embodiment is circular, and the drilling position and number of the outer cladding steel plate of the experimental member are determined and drilled according to the temperature field measurement position, and the position and quantity of the thermocouple measuring points along the thickness direction are determined according to the measurement needs;
[0060] Arrange the thermocouples and bind them into a thermocouple bundle. The cross section of the thermocouple bundle is as follows: Figure 5 As shown, mark the position of the outer surface of the experimental component corresponding to the drilled hole on the thermocouple bundle;
[0061] Weld the fixing bracket on the outer surface of the experimental component;
[0062] First pour the concrete under the drilled hole and vibrate it compactly, and make the upper surface of the concrete flush with the lowest point of the drilled hole;
[0063] Extend th...
Embodiment 3
[0066] The cross-section of the vertical composite member used in this embodiment is I-shaped, and the drilling position of the outer steel plate of the experimental member is determined and drilled according to the temperature field measurement position, and the position and number of thermocouple measuring points along the thickness direction are determined according to the measurement needs;
[0067] Arrange the thermocouples and bind them into a thermocouple bundle. The cross section of the thermocouple bundle is as follows: Image 6 As shown, measure the distance from the measuring point to the outer surface of the drilled steel plate on the thermocouple and mark it;
[0068] Weld the fixing bracket on the outer surface of the experimental component;
[0069] First pour the concrete under the drilled hole and vibrate it compactly, and make the upper surface of the concrete flush with the lowest point of the drilled hole;
[0070] Extend the thermocouple bundle from the d...
PUM
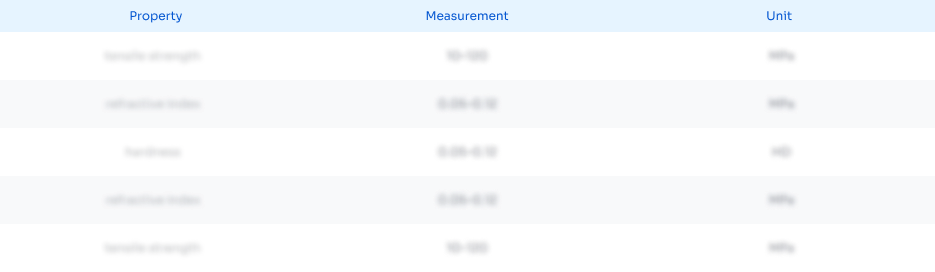
Abstract
Description
Claims
Application Information

- Generate Ideas
- Intellectual Property
- Life Sciences
- Materials
- Tech Scout
- Unparalleled Data Quality
- Higher Quality Content
- 60% Fewer Hallucinations
Browse by: Latest US Patents, China's latest patents, Technical Efficacy Thesaurus, Application Domain, Technology Topic, Popular Technical Reports.
© 2025 PatSnap. All rights reserved.Legal|Privacy policy|Modern Slavery Act Transparency Statement|Sitemap|About US| Contact US: help@patsnap.com