Molding method of casting
A casting and parting surface technology, which is applied to the modeling field of castings, can solve the problems of high casting cost and long cycle of castings, and achieve the effects of reducing casting cost, simple steps and shortening production cycle.
- Summary
- Abstract
- Description
- Claims
- Application Information
AI Technical Summary
Problems solved by technology
Method used
Image
Examples
Embodiment 1
[0032] Embodiment one: a molding method of a casting, specifically comprising the following steps:
[0033] Molding scheme design: use the end face of the casting as the parting surface to divide the upper box and the lower box for molding; according to the casting structure and modeling accuracy, the overall sand core of the casting is divided into the main sand core 100 and the tire plate sand core 200.
[0034] Sand core production: 3D printing is used to make each sand core, and the positioning reference for placing the main sand core 100 is set on the tire plate sand core 200, wherein the positioning reference follows the end face contour of the casting; the main sand core 100 is divided into inner ring sand cores 110 and outer ring sand core 120, the inner ring sand core 110 is used to form the inner ring structure of the casting, and the outer ring sand core 120 is used to form the outer ring structure of the casting; the tire plate sand core 200 is divided into a refere...
Embodiment 2
[0039] Embodiment 2: On the basis of the steps in Embodiment 1, the inner ring sand core 110 is divided into several inner ring sand core modules 111, and the outer ring sand core 120 is divided into several outer ring sand core modules 121, and the cores are laid according to the sequence Numbering; the base core 210, each rotating core 220, and the bottom surface of the closed core 230 are provided with an anti-falling structure 240, a gate positioning structure 250, and a reinforcing rib 260; specifically, the reinforcing rib 260 is set in a grid shape to increase contact with the sand area to increase the strength of the rib 260.
[0040] It should be noted that when making sand cores, it is determined according to the printing range of the printer that the inner ring sand core 110 and the outer ring sand core 120 are divided into a reasonable number of corresponding sand core modules according to a certain angle to meet production requirements; The embodiment mainly relat...
PUM
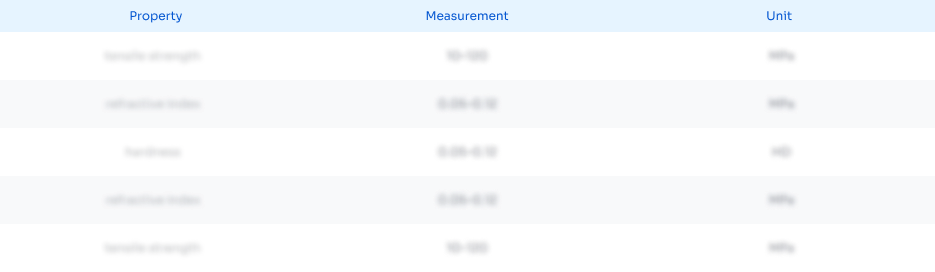
Abstract
Description
Claims
Application Information

- R&D
- Intellectual Property
- Life Sciences
- Materials
- Tech Scout
- Unparalleled Data Quality
- Higher Quality Content
- 60% Fewer Hallucinations
Browse by: Latest US Patents, China's latest patents, Technical Efficacy Thesaurus, Application Domain, Technology Topic, Popular Technical Reports.
© 2025 PatSnap. All rights reserved.Legal|Privacy policy|Modern Slavery Act Transparency Statement|Sitemap|About US| Contact US: help@patsnap.com