Method for recovering vanadium from calcified vanadium extraction tailings
A technology for extracting vanadium tailings and precipitating vanadium is applied in the field of recovering vanadium and can solve the problems of large loss of vanadium, inability to recover vanadium, loss of vanadium and the like
- Summary
- Abstract
- Description
- Claims
- Application Information
AI Technical Summary
Problems solved by technology
Method used
Examples
Embodiment 1
[0071] (1) the 1 in 1000g table 1 # Calcified vanadium extraction tailings, 20g of calcium sulfite were added to 1500mL of water for beating, and then sulfuric acid was added for leaching. The leaching pH value was 0.8, the leaching time was 10min, and the leaching temperature was 25°C. The pH value is adjusted to 2.5, then solid-liquid separation, obtains 1047g residue and leachate, in residue, V 2 o 5 The content is 0.95% by weight, and the vanadium transfer leaching rate is 65.53%;
[0072] (2) Utilize magnesium carbonate to adjust the pH value of the leachate to 6.8 to carry out vanadium precipitation, then filter to obtain vanadium precipitate and waste water, the concentration of TV in the waste water is 0.04g / L;
[0073] (3) according to the liquid-solid ratio of sodium hydroxide solution and vanadium deposit, be 15.6mL / g to add the sodium hydroxide solution (the content of NaOH is 80g / L) of 400mL in vanadium deposit, feed air, in stirring Under the conditions, react...
Embodiment 2
[0078] (1) the 2 in 1000g table 1 # Calcified vanadium extraction tailings and 19g of calcium sulfite were added to 1500mL of water for beating, and then sulfuric acid was added for leaching. The leaching pH value was 0.9, the leaching time was 20min, and the leaching temperature was 25°C. The pH value is adjusted to 2.7, followed by solid-liquid separation, to obtain 1043g residue and leachate, V in the residue 2 o 5 The content is 0.81% by weight, and the vanadium transfer leaching rate is 65.33%;
[0079] (2) Utilize magnesium carbonate to adjust the pH value of the leachate to 6.7 to carry out vanadium precipitation, then filter to obtain vanadium precipitate and waste water, the concentration of TV in the waste water is 0.04g / L;
[0080](3) be 13.5mL / g according to the liquid-solid ratio of sodium hydroxide solution and vanadium deposit, add the sodium hydroxide solution (the content of NaOH is 100g / L) of 300mL in the vanadium deposit, pass into oxygen, in stirring Rea...
Embodiment 3
[0085] (1) the 3 in 1000g table 1 # Calcified vanadium extraction tailings and 23.5g calcium sulfite were added to 1500mL water for beating, and then sulfuric acid was added for leaching. The pH value of leaching was 0.6, the leaching time was 10min, and the leaching temperature was 25°C. The pH value is adjusted to 2.8, then solid-liquid separation, obtains 1055g residue and leachate, in the residue V 2 o 5 The content is 0.87% by weight, and the vanadium transfer leaching rate is 68.89%;
[0086] (2) Utilize magnesium carbonate to adjust the pH value of the leachate to 6.5 to carry out vanadium precipitation, then filter to obtain vanadium precipitate and waste water, the concentration of TV in the waste water is 0.06g / L;
[0087] (3) According to the liquid-solid ratio of the sodium hydroxide solution and the vanadium precipitate, it is 14mL / g to add 400mL of sodium hydroxide solution (the content of NaOH is 100g / L) in the vanadium precipitate, feed into the air, under th...
PUM
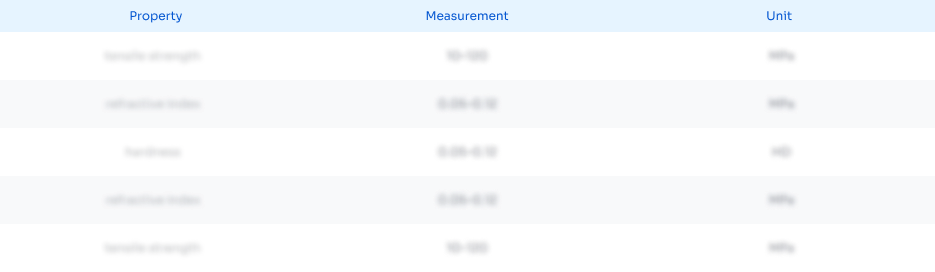
Abstract
Description
Claims
Application Information

- R&D
- Intellectual Property
- Life Sciences
- Materials
- Tech Scout
- Unparalleled Data Quality
- Higher Quality Content
- 60% Fewer Hallucinations
Browse by: Latest US Patents, China's latest patents, Technical Efficacy Thesaurus, Application Domain, Technology Topic, Popular Technical Reports.
© 2025 PatSnap. All rights reserved.Legal|Privacy policy|Modern Slavery Act Transparency Statement|Sitemap|About US| Contact US: help@patsnap.com