Denitration catalyst as well as preparation method and application thereof
A denitration catalyst and molecular sieve technology, applied in the field of catalysis, can solve the problems of good low temperature activity, no sulfur resistance, poor low temperature activity, etc., and achieve the effects of improving electron migration, excellent denitration activity, and excellent catalytic activity.
- Summary
- Abstract
- Description
- Claims
- Application Information
AI Technical Summary
Problems solved by technology
Method used
Image
Examples
Embodiment 1
[0116] With 12.3g of 50wt% manganese nitrate solution, 4.6g Cu(NO 3 ) 2 ·6H 2 O, 1.5g La(NO 3 ) 3 ·6H 2 Dissolve O in 30g deionized water, stir evenly, add 10g ZSM-5 zeolite molecular sieve, then stir at room temperature for 3h, evaporate the water to dry the solid obtained at 110°C for 10h, then roast at 540°C for 3h to obtain the Mn-Cu-La catalyst (denoted as Mn-Cu-La / ZSM-5).
Embodiment 2
[0118] With 12.3g of 50wt% manganese nitrate solution, 4.6g Cu(NO 3 ) 2 ·6H 2 O, 1.5g La(NO 3 ) 3 ·6H 2 Dissolve O in 30g deionized water, stir evenly, add 10g ZSM-5 zeolite molecular sieve, then stir at room temperature for 3h, evaporate the water to dry the solid obtained at 110°C for 10h, then roast at 540°C for 3h to obtain the Mn-Cu-La catalyst . The obtained 5g Mn-Cu-La catalyst was placed in a mixed solution consisting of 2g silica sol, 1g titanium dioxide, 1g tetrapropylammonium hydroxide solution and 49g deionized water, and the solid obtained by crystallization at 170°C for 48h was subjected to Filtration, drying, and roasting, the roasting condition is 540° C. for 3 hours, to obtain the denitration catalyst precursor. Add the denitration catalyst precursor to 0.025mol / L NaOH alkali solution, the solid-to-liquid ratio is 1:10 (g:ml), stir, transfer the slurry to a hydrothermal synthesis kettle, and put it in an oven (170°C) for Hydrothermal recrystallization 2...
Embodiment 3
[0122] With 12.3g of 50wt% manganese nitrate solution, 4.6g Cu(NO 3 ) 2 ·6H 2 O, 1.5g La(NO 3 ) 3 ·6H 2 Dissolve O in 30g deionized water, stir evenly, add 10g ZSM-5 zeolite molecular sieve, then stir at room temperature for 3h, evaporate the water to dry the solid obtained at 110°C for 10h, then roast at 540°C for 3h to obtain the Mn-Cu-La catalyst . The obtained 5g Mn-Cu-La catalyst was placed in a mixed solution consisting of 0.6g white carbon black, 1g titanium dioxide, 1gTPAOH (tetrapropylammonium hydroxide) solution and 49g deionized water, and crystallized at 170°C for 48h , the obtained solid was filtered, dried and calcined at 540° C. for 3 h to obtain a denitration catalyst precursor. Add the denitrification catalyst precursor to 0.075mol / L TPAOH solution, the solid-to-liquid ratio is 1:10 (g:ml), stir, transfer the slurry to a hydrothermal synthesis kettle, put it in an oven (170°C) for hydrothermal Thermal recrystallization for 24h. The solid was isolated b...
PUM
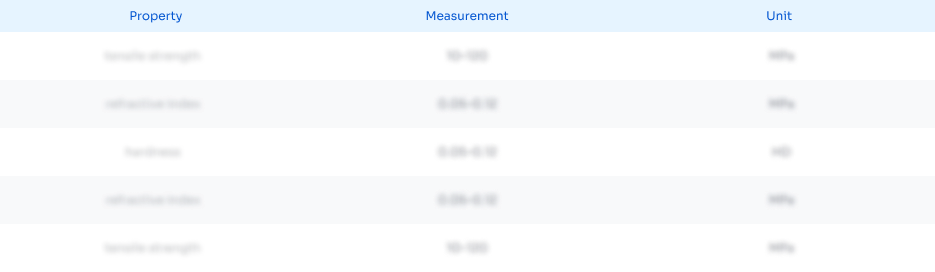
Abstract
Description
Claims
Application Information

- R&D Engineer
- R&D Manager
- IP Professional
- Industry Leading Data Capabilities
- Powerful AI technology
- Patent DNA Extraction
Browse by: Latest US Patents, China's latest patents, Technical Efficacy Thesaurus, Application Domain, Technology Topic, Popular Technical Reports.
© 2024 PatSnap. All rights reserved.Legal|Privacy policy|Modern Slavery Act Transparency Statement|Sitemap|About US| Contact US: help@patsnap.com