Inertial sensor correction verification method based on finite element analysis model
An inertial sensor and analysis model technology, applied in the field of inertial sensors, can solve the problems of insufficient accuracy of inertial sensors and unsatisfactory LPF performance, and achieve the effect of reducing electrostatic force requirements and reducing electrostatic force.
- Summary
- Abstract
- Description
- Claims
- Application Information
AI Technical Summary
Problems solved by technology
Method used
Image
Examples
Embodiment Construction
[0034] In order to have a clearer understanding of the technical features, purposes and effects of the present invention, the specific implementation manners of the present invention will now be described in detail with reference to the accompanying drawings.
[0035] Embodiments of the present invention provide a verification method, device and storage device for inertial sensor correction based on a finite element analysis model. The size of the existing inertial sensor is 46mm*46mm*46mm, and the finite element analysis method is to simulate the modified electrostatic model of the improved inertial sensor with finite element simulation software.
[0036] Please refer to figure 1 , figure 1 It is a flowchart of a verification method for inertial sensor correction based on a finite element analysis model in an embodiment of the present invention, specifically including the following steps:
[0037] S1: Adjust the size of the inspection mass in the existing inertial sensor an...
PUM
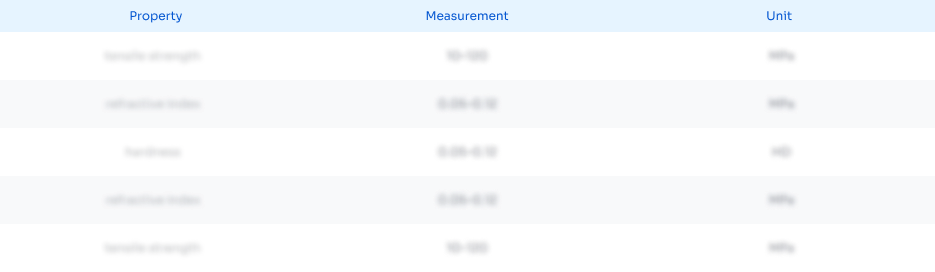
Abstract
Description
Claims
Application Information

- R&D Engineer
- R&D Manager
- IP Professional
- Industry Leading Data Capabilities
- Powerful AI technology
- Patent DNA Extraction
Browse by: Latest US Patents, China's latest patents, Technical Efficacy Thesaurus, Application Domain, Technology Topic, Popular Technical Reports.
© 2024 PatSnap. All rights reserved.Legal|Privacy policy|Modern Slavery Act Transparency Statement|Sitemap|About US| Contact US: help@patsnap.com