Micromechanical sensor and method for producing a micromechanical sensor
A micro-mechanical and sensor technology, applied in the field of manufacturing micro-mechanical sensors, can solve problems such as unsatisfactory, achieve the effect of reducing electrostatic force, reducing electrostatic force, and improving sensitivity and resilience
- Summary
- Abstract
- Description
- Claims
- Application Information
AI Technical Summary
Problems solved by technology
Method used
Image
Examples
Embodiment Construction
[0046] The core of the invention is the use of masses for micromechanical sensors (such as z-acceleration sensors, lateral acceleration sensors, rotational rate sensors, etc.) that are not perforated (or only weakly perforated) at least in sections , in which, unlike known micromechanical sensors, the distance to the underlying layer (for example the base body) in the region of the mass is significantly increased. Due to the increased spacing compared to the prior art, electrostatic interactions with underlying layers can be minimized and, moreover, the extrusion film damping in the region of the additional mass does not compare to lateral The damping of the sensor is designed disproportionately high. The non-perforated additional mass is advantageously combined with a fully differential electrode arrangement of the isometric rod in order to achieve its low susceptibility to bending relative to the base body and its high capacitance density (effective capacitance per unit area...
PUM
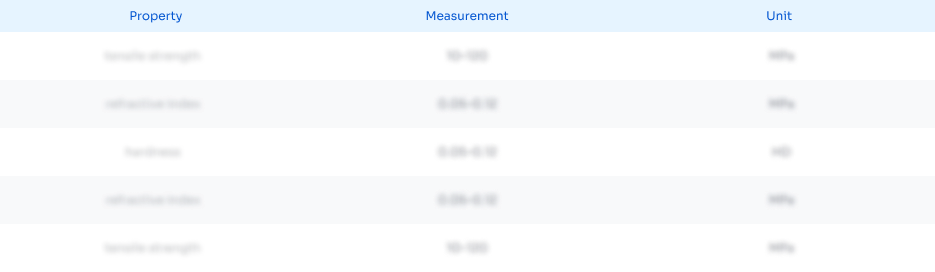
Abstract
Description
Claims
Application Information

- Generate Ideas
- Intellectual Property
- Life Sciences
- Materials
- Tech Scout
- Unparalleled Data Quality
- Higher Quality Content
- 60% Fewer Hallucinations
Browse by: Latest US Patents, China's latest patents, Technical Efficacy Thesaurus, Application Domain, Technology Topic, Popular Technical Reports.
© 2025 PatSnap. All rights reserved.Legal|Privacy policy|Modern Slavery Act Transparency Statement|Sitemap|About US| Contact US: help@patsnap.com