Batching machine for thermal insulation production of rock wool
A technology of batching machine and rock wool, applied in the field of batching machine for rock wool thermal insulation production, can solve the problems of low mixing degree, low efficiency, bloated mechanism, etc., and achieve the effect of smooth mixing, high efficiency and simplified mechanism
- Summary
- Abstract
- Description
- Claims
- Application Information
AI Technical Summary
Problems solved by technology
Method used
Image
Examples
Embodiment 1
[0028] refer to Figure 1-4 , a batching machine for rock wool insulation production, including a raw material bin A and a centralized discharge pipe C, there are multiple raw material bins A, and the bottom of the raw material bin A is provided with a feeding mechanism B, and the bottom of the feeding mechanism B is connected to the centralized The discharge pipes C are fixedly connected with the feed pipe D, and the top of the concentrated discharge pipe C is divergently provided with connection holes. The central discharge pipe C is vertically rotated and installed with a spiral discharge shaft E. Between each raw material warehouse A There is a linkage mechanism F that drives each reclaiming mechanism B to run synchronously. The linkage mechanism F drives the reclaiming mechanism B, and the raw materials in each raw material bin A are introduced into the discharge pipe C through the guide pipe D at intervals. The screw discharge shaft E in the discharge pipe C also rotates...
Embodiment 2
[0033] like Figure 1-4 As shown, this embodiment is basically the same as Embodiment 1. Preferably, the screw discharge shaft E is located in the centralized discharge pipe C, and the top of the screw discharge shaft E is coaxially fixedly connected with an oblong shaft 17, and the oblong shaft 17 The top end passes through the top of the centralized discharge pipe C and is coaxially fixedly connected with the bottom side of the turntable 6 , and a reinforcing rib 18 is provided between the long circular axis 17 and the turntable 6 .
[0034] In this embodiment, through the setting of the oblong shaft 17, it is possible to drive the screw discharge shaft through the turntable 6 and the oblong shaft 17 to concentrate the discharge pipe C while driving the rotating drum 7 to rotate and carry out the interval blanking of the material. The internal rotation ensures the smoothness of blanking.
Embodiment 3
[0036] like Figure 1-4 As shown, this embodiment is basically the same as Embodiment 1. Preferably, the top of the track pole 8 is fixedly connected with a top platform 14, and a motor 15 is fixedly installed on the top platform 14, and the output shaft of the motor 15 extends to the drive shaft. The inner side of the cylinder 7 is fixedly connected with the inner wall of the driving drum 7 with several umbrella shafts 16 arranged in a divergent manner.
[0037] In this embodiment, the umbrella shaft 16 outside the output shaft of the motor 15 drives the entire drive drum 7 to rotate, and the turntable 6 and the oblong shaft 17 at the bottom of the drive drum 7 also rotate accordingly.
PUM
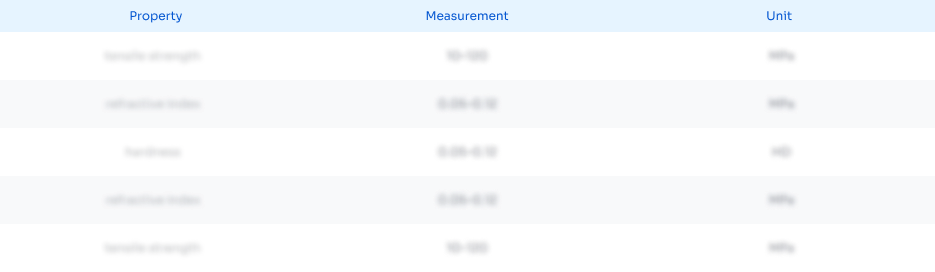
Abstract
Description
Claims
Application Information

- Generate Ideas
- Intellectual Property
- Life Sciences
- Materials
- Tech Scout
- Unparalleled Data Quality
- Higher Quality Content
- 60% Fewer Hallucinations
Browse by: Latest US Patents, China's latest patents, Technical Efficacy Thesaurus, Application Domain, Technology Topic, Popular Technical Reports.
© 2025 PatSnap. All rights reserved.Legal|Privacy policy|Modern Slavery Act Transparency Statement|Sitemap|About US| Contact US: help@patsnap.com