Blending system and mixing process of isoprene rubber and brominated butyl rubber
A technology of brominated butyl rubber and isoprene rubber, which is applied in the field of rubber, can solve the problems of self-sealing performance and degradation of rubber shavings produced by rubber stoppers, and achieve stable mixing curves, good rubber dispersion, and The effect of excellent vulcanization performance
- Summary
- Abstract
- Description
- Claims
- Application Information
AI Technical Summary
Problems solved by technology
Method used
Image
Examples
Embodiment 1
[0026] Masterbatch: bromobutyl rubber 2.5kg, titanium dioxide 1kg, reinforcing agent carbon black 0.02kg, vulcanizing agent phenolic resin 2.5kg;
[0027] Mixed rubber: bromobutyl rubber 17.5kg, isoprene rubber 30kg, clay 37.5kg, softener modified polyethylene 0.5kg and stearic acid 0.75kg, accelerator zinc oxide 2.5kg, antioxidant 1076 0.5 kg.
[0028] A mixing process of a blend system of isoprene rubber and bromobutyl rubber, the concrete process steps are as follows:
[0029] (1) Firstly, the bromobutyl rubber in the masterbatch is pressed and kneaded with titanium dioxide, reinforcing agent and vulcanizing agent until the rubber is discharged at 90°C to produce the masterbatch;
[0030] (2) In the process of mixing raw rubber and masticating, first add brominated butyl rubber and then put it into pottery clay, and carry out 2 minutes of pressing and banburying;
[0031] (3) drop into isoprene rubber, softener, promotor, antioxidant in step (2) again and carry out 2min c...
Embodiment 2
[0036] Masterbatch: bromobutyl rubber 1.875kg, titanium dioxide 0.5kg, reinforcing agent carbon black 0.01kg, vulcanizing agent phenolic resin 2kg;
[0037] Mixed rubber: bromobutyl rubber 13.125kg, isoprene rubber 25kg, clay 32.5kg, softener modified polyethylene 0.4kg and stearic acid 0.6kg, accelerator zinc oxide 2kg, antioxidant 1076 0.4kg .
[0038] A mixing process of a blend system of isoprene rubber and bromobutyl rubber, the concrete process steps are as follows:
[0039] (1) Firstly, the bromobutyl rubber in the masterbatch is pressed and kneaded with titanium dioxide, reinforcing agent and vulcanizing agent until the rubber is discharged at 90°C to produce the masterbatch;
[0040] (2) In the process of mixing raw rubber and masticating, first add brominated butyl rubber and then put it into pottery clay, and carry out 2 minutes of pressing and banburying;
[0041] (3) drop into isoprene rubber, softener, promotor, antioxidant in step (2) again and carry out 2min ...
Embodiment 3
[0046] Masterbatch: bromobutyl rubber 3.125kg, titanium dioxide 1.5kg, reinforcing agent carbon black 0.03kg, vulcanizing agent phenolic resin 3kg;
[0047] Mixed rubber: bromobutyl rubber 21.875kg, isoprene rubber 35kg, clay 42.5kg, softener modified polyethylene 0.6kg and stearic acid 0.9kg, accelerator zinc oxide 3kg, antioxidant 1076 0.6kg .
[0048]A mixing process of a blend system of isoprene rubber and bromobutyl rubber, the concrete process steps are as follows:
[0049] (1) Firstly, the bromobutyl rubber in the masterbatch is pressed and kneaded with titanium dioxide, reinforcing agent and vulcanizing agent until the rubber is discharged at 90°C to produce the masterbatch;
[0050] (2) In the process of mixing raw rubber and masticating, first add brominated butyl rubber and then put it into pottery clay, and carry out 2 minutes of pressing and banburying;
[0051] (3) drop into isoprene rubber, softener, promotor, antioxidant in step (2) again and carry out 2min c...
PUM
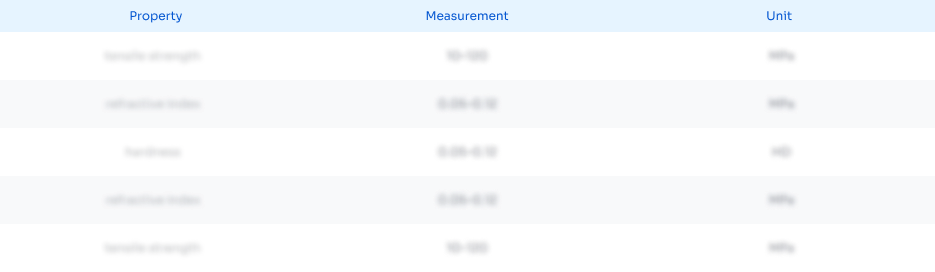
Abstract
Description
Claims
Application Information

- R&D
- Intellectual Property
- Life Sciences
- Materials
- Tech Scout
- Unparalleled Data Quality
- Higher Quality Content
- 60% Fewer Hallucinations
Browse by: Latest US Patents, China's latest patents, Technical Efficacy Thesaurus, Application Domain, Technology Topic, Popular Technical Reports.
© 2025 PatSnap. All rights reserved.Legal|Privacy policy|Modern Slavery Act Transparency Statement|Sitemap|About US| Contact US: help@patsnap.com