Multi-laser system lap joint correction method for additive manufacturing equipment
A technology of additive manufacturing and calibration method, which is applied in the field of additive manufacturing, can solve problems such as the inability to quickly judge whether the overlapping effect is consistent, the inability to quickly confirm the overlapping effect, and the long debugging time span, so as to achieve convenient overlapping debugging verification, The effect of short debugging cycle and low cost
- Summary
- Abstract
- Description
- Claims
- Application Information
AI Technical Summary
Problems solved by technology
Method used
Image
Examples
Embodiment Construction
[0039] In order to make the purpose, technical solution and advantages of the present application clearer, the present application will be further described in detail below in conjunction with the accompanying drawings and embodiments. It should be understood that the specific embodiments described here are only used to explain the present application, and are not intended to limit the present application.
[0040] Such as figure 1 As shown, the present invention provides a multi-laser system lap correction method for additive manufacturing equipment, comprising the following steps:
[0041] Step S1: placing the detection board with at least one film on the substrate of the additive manufacturing equipment, and making the distance between the surface of the detection board and the bottom of the scraper be 0.1-1 mm;
[0042] Preferably, the detection board can be leveled first by the substrate leveling mechanism, and then the distance between the surface of the detection board a...
PUM
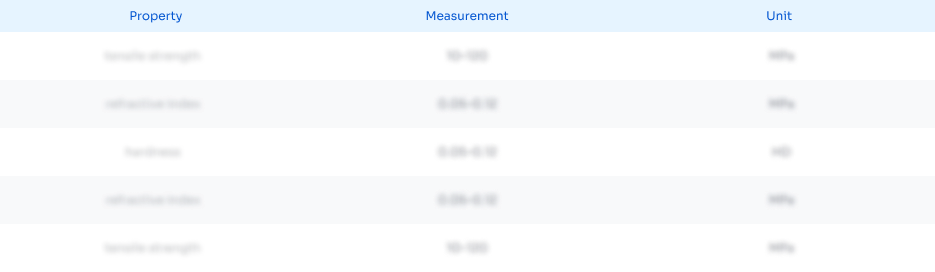
Abstract
Description
Claims
Application Information

- R&D
- Intellectual Property
- Life Sciences
- Materials
- Tech Scout
- Unparalleled Data Quality
- Higher Quality Content
- 60% Fewer Hallucinations
Browse by: Latest US Patents, China's latest patents, Technical Efficacy Thesaurus, Application Domain, Technology Topic, Popular Technical Reports.
© 2025 PatSnap. All rights reserved.Legal|Privacy policy|Modern Slavery Act Transparency Statement|Sitemap|About US| Contact US: help@patsnap.com