Cable duct bank dredging robot capable of self-adapting to shape of pipeline
A cable ducting and self-adaptive technology, applied in the field of robots, can solve problems such as poor ability to adapt to the shape of pipes, and achieve the effect of enhancing adaptability
- Summary
- Abstract
- Description
- Claims
- Application Information
AI Technical Summary
Problems solved by technology
Method used
Image
Examples
Embodiment 1
[0030] This embodiment discloses a cable pipe dredging robot capable of adapting to the shape of the pipe, such as Figure 1-Figure 6 As shown, it includes a front cabin 1 and a rear cabin 2. The front cabin is located at the front end of the robot's travel direction, and the rear cabin is located at the rear end of the robot's travel direction. The rear cabin is equipped with a drive mechanism as a power source for the robot to advance. The front cabin A cleaning mechanism is installed inside to clean up the blockages in the cable pipes. Since the peristaltic robot cannot adapt to the shape of the pipeline, this embodiment does not use the peristaltic drive mode. The front cabin and the rear cabin Universal connection is made between them, and the rear cabin is used to push the front cabin to move, so as to realize the forward movement of the whole robot. At the same time, the length of the whole robot is shortened due to the omission of the cylinder between the front cabin an...
PUM
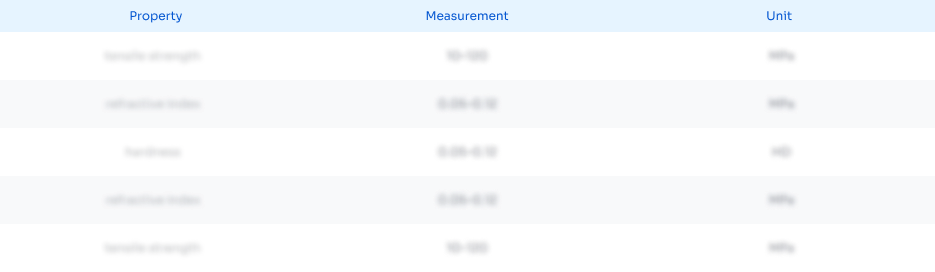
Abstract
Description
Claims
Application Information

- R&D
- Intellectual Property
- Life Sciences
- Materials
- Tech Scout
- Unparalleled Data Quality
- Higher Quality Content
- 60% Fewer Hallucinations
Browse by: Latest US Patents, China's latest patents, Technical Efficacy Thesaurus, Application Domain, Technology Topic, Popular Technical Reports.
© 2025 PatSnap. All rights reserved.Legal|Privacy policy|Modern Slavery Act Transparency Statement|Sitemap|About US| Contact US: help@patsnap.com