High-uniformity CCM continuous coating process for fuel cell
A fuel cell and coating technology, used in fuel cells, battery electrodes, devices for coating liquids on surfaces, etc. performance and service life, improved coating uniformity, and the effect of improving coating uniformity
- Summary
- Abstract
- Description
- Claims
- Application Information
AI Technical Summary
Problems solved by technology
Method used
Image
Examples
Embodiment 1
[0034] A fuel cell CCM preparation process, comprising the following steps:
[0035] (1) prepare low-concentration catalyst slurry: take by weighing 20g 70% Pt / C catalyst, 100g 10% perfluorosulfonic acid resin solution and 800g isopropanol, mix, high-speed stirring disperses, adopts vacuum defoaming to make low Concentration catalyst slurry;
[0036] (2) Preparation of high-concentration catalyst slurry: Weigh 20g of 70% Pt / C catalyst, 100g of 10% perfluorosulfonic acid resin solution, 40g of ethylene glycol and 600g of isopropanol, mix, stir at high speed to disperse, and use vacuum Defoaming to prepare high-concentration catalyst slurry;
[0037] (3) Use roll-to-roll coating equipment to place the anode low-concentration catalyst slurry and the cathode high-concentration catalyst slurry in the anode feed system and the cathode feed system, respectively;
[0038] (4) Coating the low-concentration catalyst slurry in step (1) on the A side of the proton exchange membrane by a...
Embodiment 2
[0040] (1) prepare low-concentration catalyst slurry: take by weighing 20g 40% Pt / C catalyst, 200g 5% perfluorosulfonic acid resin solution and 2000g isopropanol, mix, high-speed stirring disperses, adopts vacuum defoaming to make low Concentration catalyst slurry;
[0041] (2) Prepare high-concentration catalyst slurry: take by weighing 20g of 40% Pt / C catalyst, 200g of 5% perfluorosulfonic acid resin solution, 120g of glycerol and 1000g of isopropanol, mix, stir at high speed to disperse, and use vacuum Defoaming to prepare high-concentration catalyst slurry;
[0042] (3) Use roll-to-roll coating equipment to place the anode low-concentration catalyst slurry and the cathode high-concentration catalyst slurry in the anode feed system and the cathode feed system, respectively;
[0043] (4) The low-concentration catalyst slurry in step (1) is coated on the A side of the proton exchange membrane by adopting the process parameters of coating speed 5m / min and coating wet thicknes...
Embodiment 3
[0045] (1) prepare low-concentration catalyst slurry: take by weighing 20g 60% Pt / C catalyst, 120g 5% perfluorosulfonic acid resin solution and 1800g isopropanol, mix, high-speed stirring disperses, adopts vacuum defoaming to make low Concentration catalyst slurry;
[0046] (2) Preparation of high-concentration catalyst slurry: Weigh 20g of 60% Pt / C catalyst, 160g of 5% perfluorosulfonic acid resin solution, 80g of ethyl acetate and 800g of isopropanol, mix, stir at high speed to disperse, and use vacuum Defoaming to prepare high-concentration catalyst slurry;
[0047] (3) Use roll-to-roll coating equipment to place the anode low-concentration catalyst slurry and the cathode high-concentration catalyst slurry in the anode feed system and the cathode feed system, respectively;
[0048] (4) Coating the low-concentration catalyst slurry in step (1) on the A side of the proton exchange membrane by adopting the technological parameters of coating speed 8m / min and coating wet thick...
PUM
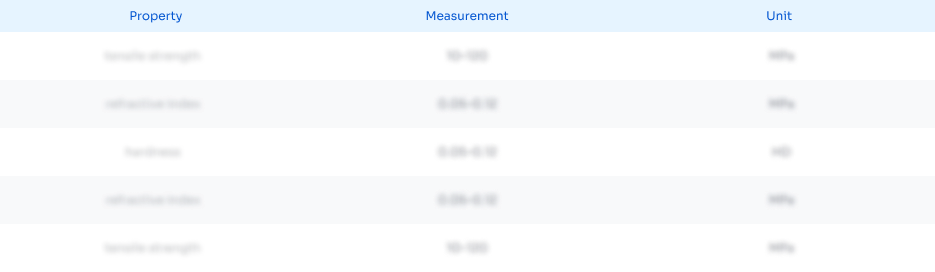
Abstract
Description
Claims
Application Information

- R&D
- Intellectual Property
- Life Sciences
- Materials
- Tech Scout
- Unparalleled Data Quality
- Higher Quality Content
- 60% Fewer Hallucinations
Browse by: Latest US Patents, China's latest patents, Technical Efficacy Thesaurus, Application Domain, Technology Topic, Popular Technical Reports.
© 2025 PatSnap. All rights reserved.Legal|Privacy policy|Modern Slavery Act Transparency Statement|Sitemap|About US| Contact US: help@patsnap.com