Auxiliary transportation robot positioning method and system in dynamic complex mine environment
A robot positioning and auxiliary transportation technology, which is applied in the direction of instruments, earthwork drilling, wellbore/well components, etc., can solve the problems of measurement loss, high cost, and affecting positioning accuracy, so as to reduce positioning errors and achieve high positioning accuracy , The effect of low positioning cost
- Summary
- Abstract
- Description
- Claims
- Application Information
AI Technical Summary
Problems solved by technology
Method used
Image
Examples
Embodiment Construction
[0032] The present invention will be further described below in conjunction with the accompanying drawings.
[0033] like figure 1 and figure 2 As shown, the present invention is a high-precision and robust positioning method of an auxiliary transport robot in a strong interference mine environment. First, the distance from the auxiliary transport robot 7 to the UWB anchor point (the coordinates of the UWB anchor point are known) is measured, and then the distance value is compared with The IMU acceleration information provided by the IMU is fused using the extended Kalman filter principle to obtain the high-precision and robust position information of the assisted transport robot 7, which includes the following steps:
[0034] 1) Obtain the UWB distance information between the auxiliary transportation robot 7 and the UWB anchor point whose coordinates are known, and the IMU acceleration information of the auxiliary transportation robot 7; the UWB distance information is use...
PUM
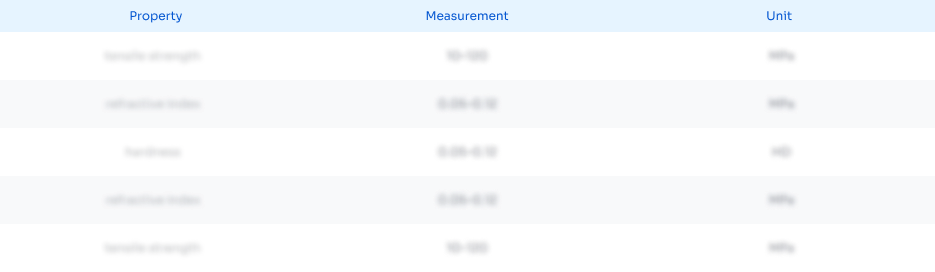
Abstract
Description
Claims
Application Information

- R&D Engineer
- R&D Manager
- IP Professional
- Industry Leading Data Capabilities
- Powerful AI technology
- Patent DNA Extraction
Browse by: Latest US Patents, China's latest patents, Technical Efficacy Thesaurus, Application Domain, Technology Topic, Popular Technical Reports.
© 2024 PatSnap. All rights reserved.Legal|Privacy policy|Modern Slavery Act Transparency Statement|Sitemap|About US| Contact US: help@patsnap.com