Rotary position sensor
A technology of rotating position and sensor, which is applied in the field of position sensing, can solve problems such as sensor malfunction, sensor failure, loss of support, etc., achieve good insulation and adhesion, eliminate the influence of temperature, and achieve long-term use effects
- Summary
- Abstract
- Description
- Claims
- Application Information
AI Technical Summary
Problems solved by technology
Method used
Image
Examples
Embodiment
[0038] Example: Rotary position sensor such as Figure 1 to Figure 7 As shown, it includes a front housing 1, a rear housing 2 affixed to the front housing 1, and a controller 4 (the controller 4 adopts a PLC single-chip microcomputer); the front housing 1 includes a base block 5, a cylindrical portion 6, a support block 7 and 2 arc-shaped plates 8 symmetrically arranged and fixed to the cylindrical part 6; The top end is affixed; the use of the arc plate 8 helps to connect the cylindrical part 6 with the support block 7 and the base block 5 respectively; the use of the cylindrical part 6 helps to connect the rotating body 3, the linkage body 13 and the screw rod 14 , so that the rotational motion can be transmitted to the screw 14 and the nut 15 , so that the rotational position can be determined through the relative movement between the screw 14 and the nut 15 .
[0039]The end surface of the support block 7 close to the rear housing 2 is fixedly connected with a convex fix...
PUM
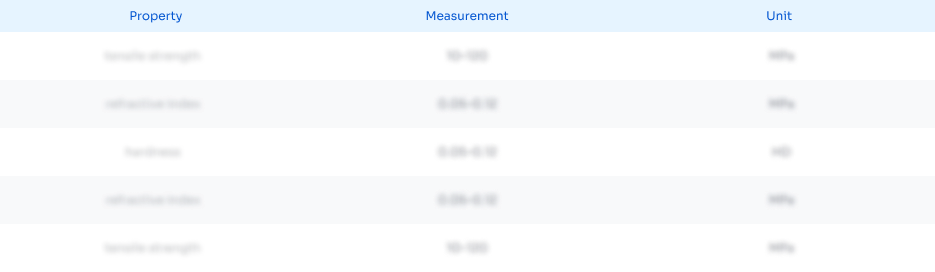
Abstract
Description
Claims
Application Information

- Generate Ideas
- Intellectual Property
- Life Sciences
- Materials
- Tech Scout
- Unparalleled Data Quality
- Higher Quality Content
- 60% Fewer Hallucinations
Browse by: Latest US Patents, China's latest patents, Technical Efficacy Thesaurus, Application Domain, Technology Topic, Popular Technical Reports.
© 2025 PatSnap. All rights reserved.Legal|Privacy policy|Modern Slavery Act Transparency Statement|Sitemap|About US| Contact US: help@patsnap.com