High-efficiency welding method for large perforated flange and thick-wall pipe
A welding method and high-efficiency technology, applied in welding equipment, welding equipment, welding accessories, etc., can solve the problems of unfavorable cost, increased labor hours, high repair rate, and reduce repair waste, save expenses, work efficiency and output. Efficiency improvement effect
- Summary
- Abstract
- Description
- Claims
- Application Information
AI Technical Summary
Problems solved by technology
Method used
Image
Examples
Embodiment Construction
[0051] The specific implementation manner of the present invention will be described below in conjunction with the accompanying drawings.
[0052] Such as Figure 1 to Figure 3 As shown, a kind of high-efficiency welding method of large-scale banded flange and thick-walled pipe of the present invention comprises the following steps:
[0053] S1: Place the flange 2 on the tire rack; the tire rack includes two rollers 3 arranged on the support; the flange 2 is placed on the two rollers 3;
[0054] S2: The flange 2 and the steel pipe 1 are positioned and connected by the code plate welded on the inner wall of the flange 2 and the steel pipe 1;
[0055] S3: a flame heating plate 4 is fixedly installed near the joint between the flange 2 and the steel pipe 1;
[0056] S4: Control the flame heating plate 4 to heat the connection between flange 2 and steel pipe 1 while turning flange 2 and steel pipe 1 until the temperature at the connection between flange 2 and steel pipe 1 is T1,...
PUM
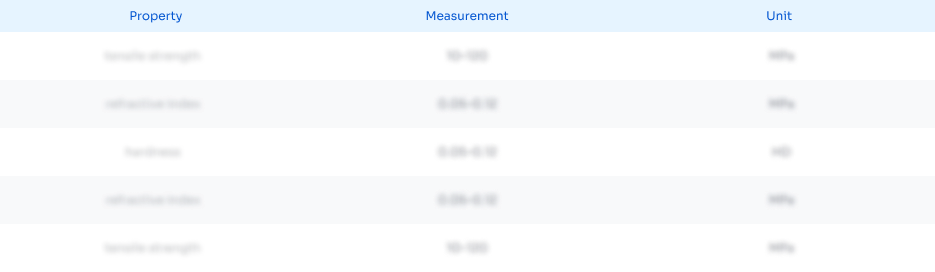
Abstract
Description
Claims
Application Information

- R&D
- Intellectual Property
- Life Sciences
- Materials
- Tech Scout
- Unparalleled Data Quality
- Higher Quality Content
- 60% Fewer Hallucinations
Browse by: Latest US Patents, China's latest patents, Technical Efficacy Thesaurus, Application Domain, Technology Topic, Popular Technical Reports.
© 2025 PatSnap. All rights reserved.Legal|Privacy policy|Modern Slavery Act Transparency Statement|Sitemap|About US| Contact US: help@patsnap.com