Preparation method of permanent magnet synchronous motor rotor
A permanent magnet synchronous motor and rotor technology, which is used in the manufacture of motor generators, stator/rotor bodies, electrical components, etc., can solve the problems of motor iron loss, rotor temperature rise, and slot bar bending, etc., to improve quality. and service life, improve guiding reliability, and avoid the effect of circumferential rotation
- Summary
- Abstract
- Description
- Claims
- Application Information
AI Technical Summary
Problems solved by technology
Method used
Image
Examples
Embodiment Construction
[0025] Combine below Figure 1~6 Embodiments of the present invention are described in detail.
[0026] The preparation method of the rotor of the permanent magnet synchronous motor is to form the iron core 1 by laminating and pressing the punching sheets first, and then install the rotating shaft 2 on the iron core 1 by shrinking the sleeve. The sample rod 3 guides and positions the punching sheet, and the flexible groove sample rod 3 is compressed synchronously with the punching sheet during the pressing process.
[0027] In the method for preparing the rotor of the permanent magnet synchronous motor described above, the flexible groove-like rod 3 is used for guidance and positioning during the stacking process of the punching sheets. pressure, the length of the flexible groove-like rod protruding from the lower die base is greater than the total height of the stacked punches, so that the punches laminated to the top will also form a guiding and positioning cooperation with...
PUM
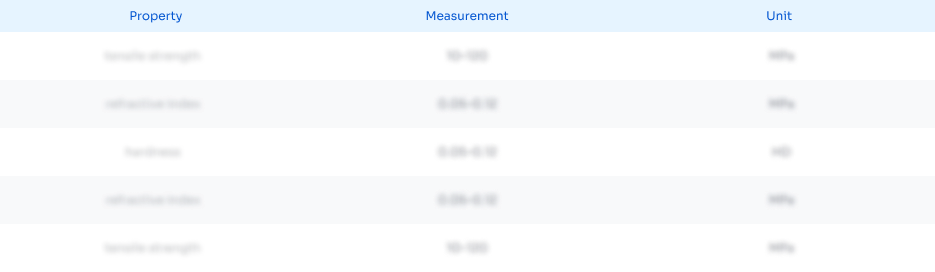
Abstract
Description
Claims
Application Information

- Generate Ideas
- Intellectual Property
- Life Sciences
- Materials
- Tech Scout
- Unparalleled Data Quality
- Higher Quality Content
- 60% Fewer Hallucinations
Browse by: Latest US Patents, China's latest patents, Technical Efficacy Thesaurus, Application Domain, Technology Topic, Popular Technical Reports.
© 2025 PatSnap. All rights reserved.Legal|Privacy policy|Modern Slavery Act Transparency Statement|Sitemap|About US| Contact US: help@patsnap.com