Finite element topological structure construction method for improving calculation application efficiency of overhead line system
A topology and construction method technology, applied in special data processing applications, design optimization/simulation, instruments, etc., can solve problems such as the lack of systematic topology construction methods, achieve high computing application efficiency, reduce the error rate, application wide range of effects
- Summary
- Abstract
- Description
- Claims
- Application Information
AI Technical Summary
Problems solved by technology
Method used
Image
Examples
Embodiment 1
[0024] Embodiments of the present invention provide a method for constructing a finite element topology structure that improves the efficiency of catenary calculation and application, and constructs a topology structure for a simple suspended catenary, such as figure 1 and figure 2 As shown, it includes the following steps:
[0025] S1: Obtain the type, quantity and location of the suspension nodes; the above data is based on the actual situation of the project. For the catenary with simple suspension, the suspension nodes include the contact wire suspension node Gc and the sling suspension node Gb.
[0026] S2: Determine the number and location of connecting nodes according to the type, quantity and location of hanging nodes. The number and location of connecting nodes are based on the spacing of the same type of suspension nodes, which can be found in the design manual. Said connecting nodes comprise contact line-cable connection nodes Jcb, which are arranged on the cont...
Embodiment 2
[0030] Embodiments of the present invention provide a method for constructing a finite element topology structure that improves the efficiency of catenary calculation and application, and constructs a topology structure for a chain-type suspended catenary, such as figure 1 and image 3 As shown, it includes the following steps:
[0031] S1: Obtain the type, quantity and location of the suspension nodes; the above data is based on the actual situation of the project. For catenary suspended by chain, the suspension nodes include contact wire suspension nodes Gc and catenary cable suspension nodes Gm.
[0032] S2: According to the type, quantity and location of the suspension nodes and the design manual, determine the number and location of the connection nodes from bottom to top, that is, first determine the number and location of the connection nodes on the contact line, and then determine the number and location of the connection nodes on the catenary cable The number and lo...
Embodiment 3
[0038] Embodiments of the present invention provide a method for constructing a finite element topology structure that improves the efficiency of catenary calculation and application. It is aimed at constructing a topology structure for a Japanese-style double-chain suspension catenary, such as figure 1 and Figure 4 shown, which includes the following steps:
[0039] S1: Obtain the type, quantity and location of the suspension nodes; the above data is based on the actual situation of the project. In the catenary with Japanese-style double-chain suspension, the suspension nodes include contact wire suspension nodes Gc, catenary cable suspension nodes Gm, and sling suspension nodes Gb.
[0040] S2: According to the type, quantity and location of the suspension nodes and the design manual, determine the number and location of the connection nodes from bottom to top; Location.
[0041] The connecting nodes include contact line-hanging string connecting node Jcd, hanging string...
PUM
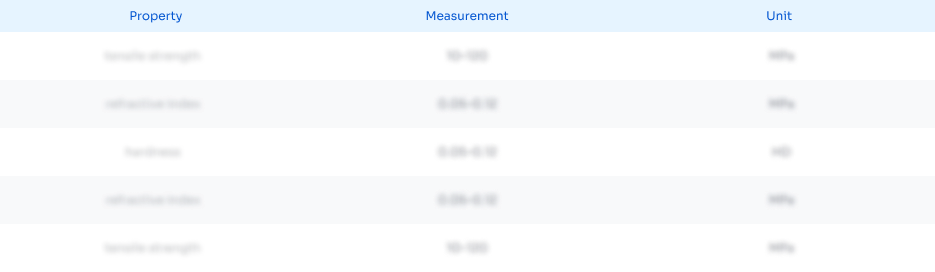
Abstract
Description
Claims
Application Information

- R&D Engineer
- R&D Manager
- IP Professional
- Industry Leading Data Capabilities
- Powerful AI technology
- Patent DNA Extraction
Browse by: Latest US Patents, China's latest patents, Technical Efficacy Thesaurus, Application Domain, Technology Topic, Popular Technical Reports.
© 2024 PatSnap. All rights reserved.Legal|Privacy policy|Modern Slavery Act Transparency Statement|Sitemap|About US| Contact US: help@patsnap.com