High-pressure oil rail argon arc welding assembly and manufacturing method thereof
A manufacturing method and argon arc welding technology, applied in manufacturing tools, arc welding equipment, welding equipment, etc., can solve the problems of waste of resources, large equipment occupancy, inability to adjust, etc., to shorten the process route, improve production efficiency, reduce The effect of occupancy
- Summary
- Abstract
- Description
- Claims
- Application Information
AI Technical Summary
Problems solved by technology
Method used
Image
Examples
Embodiment Construction
[0037] The present invention will be further described below in combination with specific embodiments. It should be understood that these examples are only used to illustrate the present invention and are not intended to limit the scope of the present invention. In addition, it should be understood that after reading the teachings of the present invention, those skilled in the art can make various changes or modifications to the present invention, and these equivalent forms also fall within the scope defined by the appended claims of the present application.
[0038] see Figure 2 to Figure 8 , the invention discloses a high-pressure oil rail argon arc welding assembly manufactured by using a manufacturing method of a high pressure oil rail argon arc welding assembly of the present invention. As shown in the figure, one of the preferred embodiments consists of a distribution pipe 100, an end cover 200, an oil inlet pipe joint 201, a bracket 201, a sensor joint 211, and an oil...
PUM
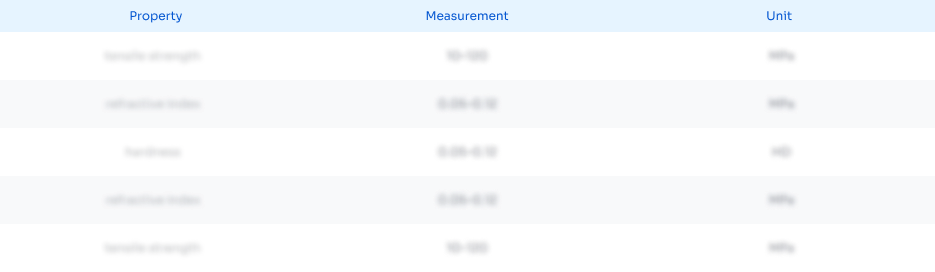
Abstract
Description
Claims
Application Information

- R&D Engineer
- R&D Manager
- IP Professional
- Industry Leading Data Capabilities
- Powerful AI technology
- Patent DNA Extraction
Browse by: Latest US Patents, China's latest patents, Technical Efficacy Thesaurus, Application Domain, Technology Topic, Popular Technical Reports.
© 2024 PatSnap. All rights reserved.Legal|Privacy policy|Modern Slavery Act Transparency Statement|Sitemap|About US| Contact US: help@patsnap.com