Tolerance optimization design method of key part of multi-axis numerical control machine tool
A numerical control machine tool and optimization design technology, applied in computer-aided design, design optimization/simulation, calculation, etc., can solve problems such as inability to optimize the distribution of tolerance parameters of key parts of machine tools
- Summary
- Abstract
- Description
- Claims
- Application Information
AI Technical Summary
Problems solved by technology
Method used
Image
Examples
Embodiment Construction
[0125] The present invention takes a five-axis elevated beam mobile gantry CNC milling machine as an example to verify the method for optimizing the distribution of tolerance parameters of key components of the five-axis CNC milling machine.
[0126] Specifically include the following steps:
[0127] Step 1: Take the five-axis CNC machine tool as an example to establish the spatial error model of the machine tool;
[0128] Based on the theory of multi-body system kinematics, the structure of the machine tool and the relationship between each body are described by topological structure graph and low-order body array table, the geometric error of the CNC machine tool is analyzed, the generalized coordinate system is established, and the relationship between adjacent bodies is used. The feature matrix expresses the positional relationship, and the homogeneous transformation matrix is used to express the relationship between multi-body systems;
[0129] Step 1.1 establishes the...
PUM
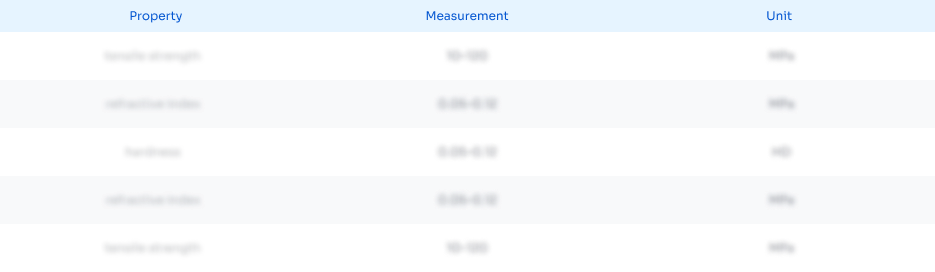
Abstract
Description
Claims
Application Information

- R&D
- Intellectual Property
- Life Sciences
- Materials
- Tech Scout
- Unparalleled Data Quality
- Higher Quality Content
- 60% Fewer Hallucinations
Browse by: Latest US Patents, China's latest patents, Technical Efficacy Thesaurus, Application Domain, Technology Topic, Popular Technical Reports.
© 2025 PatSnap. All rights reserved.Legal|Privacy policy|Modern Slavery Act Transparency Statement|Sitemap|About US| Contact US: help@patsnap.com