One-step formed plant polysaccharide and cigarette tow composite cooling section material and preparation method thereof
A plant polysaccharide and compound cooling technology, which is applied in the fields of application, tobacco, and e-liquid filter elements, can solve the problems of complex process, high cost, and poor effect, and achieve the effects of safe preparation process, delayed collapse, and controllable process
- Summary
- Abstract
- Description
- Claims
- Application Information
AI Technical Summary
Problems solved by technology
Method used
Image
Examples
Embodiment 1
[0022] A one-time molding plant polysaccharide and tobacco tow composite cooling section material, wherein the plant polysaccharide and tobacco tow mixture material includes the following components in parts by mass: 7 parts of water, 80 parts of starch, and 3 parts of konjac glucomannan , 2 parts of tobacco tow.
[0023] A method for preparing a once-molded plant polysaccharide and tobacco tow composite cooling section material, comprising the following steps:
[0024] (1) Mix and prepare plant polysaccharide and tobacco tow mixed material according to the ratio, and the initial moisture content of mixed material is 7% at this moment;
[0025] (2) The mixed material of plant polysaccharide and tobacco tow at 70°C is pushed through a screw extrusion extruder, and under the shearing action of the screw, it is extruded through an abrasive tool with a diameter of 6m at 110°C and 10MPa;
[0026] (3) Slitting and cutting into rods to obtain the composite cooling section material o...
Embodiment 2
[0030] A one-time molding plant polysaccharide and tobacco tow composite cooling section material, wherein the plant polysaccharide and tobacco tow mixture material includes the following components in parts by mass: 10 parts of water, 85 parts of starch, 5 parts of carrageenan, and 3 servings of tow.
[0031] A method for preparing a once-molded plant polysaccharide and tobacco tow composite cooling section material, comprising the following steps:
[0032] (1) Mix and prepare plant polysaccharide and tobacco tow mixed material according to the ratio, and the initial moisture content of mixed material is 10% at this moment;
[0033] (2) The mixture of plant polysaccharides and tobacco tow at 70°C is pushed through a screw extrusion extruder, and under the shearing action of the screw, it is extruded through an abrasive tool with a diameter of 7m at 125°C and 10MPa;
[0034] (3) Slitting and cutting into rods to obtain the composite cooling section material of plant polysacch...
Embodiment 3
[0038] A one-time molding plant polysaccharide and tobacco tow composite cooling section material, wherein the plant polysaccharide and tobacco tow mixture material includes the following components in parts by mass: 12 parts of water, 90 parts of starch, 5 parts of gum arabic, and 6 servings of tow.
[0039] A method for preparing a once-molded plant polysaccharide and tobacco tow composite cooling section material, comprising the following steps:
[0040] (1) Mix and prepare plant polysaccharide and tobacco tow mixed material according to the ratio, and the initial moisture content of mixed material is 12% at this moment;
[0041] (2) The mixture of plant polysaccharides and tobacco tow at 80°C is pushed through a screw extruder, and under the shearing action of the screw, it is extruded through an abrasive tool with a diameter of 8m at 135°C and 8MPa;
[0042] (3) Slitting and cutting into rods to obtain the composite cooling section material of plant polysaccharide and to...
PUM
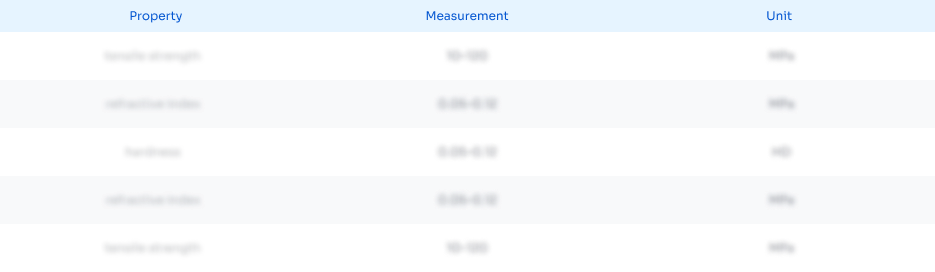
Abstract
Description
Claims
Application Information

- R&D Engineer
- R&D Manager
- IP Professional
- Industry Leading Data Capabilities
- Powerful AI technology
- Patent DNA Extraction
Browse by: Latest US Patents, China's latest patents, Technical Efficacy Thesaurus, Application Domain, Technology Topic, Popular Technical Reports.
© 2024 PatSnap. All rights reserved.Legal|Privacy policy|Modern Slavery Act Transparency Statement|Sitemap|About US| Contact US: help@patsnap.com