Robot chassis axle distance calibration method and system
A calibration method and a calibration system technology, applied in the field of robot chassis wheelbase calibration methods and systems, can solve the problems of low efficiency in calibrating the robot chassis wheelbase, solve the cumbersome manual wheelbase calibration, improve stability, and liberate labor productivity Effect
- Summary
- Abstract
- Description
- Claims
- Application Information
AI Technical Summary
Problems solved by technology
Method used
Image
Examples
Embodiment Construction
[0041] In order to explain in detail the technical content, structural features, achieved goals and effects of the technical solution, the following will be described in detail in conjunction with specific embodiments and accompanying drawings.
[0042] see image 3 The left wheel 1 of the robot is located on the left side of the robot chassis, and the right wheel 3 of the robot is located on the right side of the robot chassis. The left wheel and the right wheel can drive the robot to rotate left or right on the bearing surface. The rotation axis of the robot is perpendicular to the carrying surface, which may be the ground. Also be provided with at least one auxiliary wheel 5 (can be universal wheel) on the robot chassis, be used for the traveling of auxiliary robot. The wheelbase of the robot chassis refers to the distance between the left wheel 1 and the right wheel 3, and the error of the wheelbase will cause the error of the angular velocity (rotation angle) fed back by...
PUM
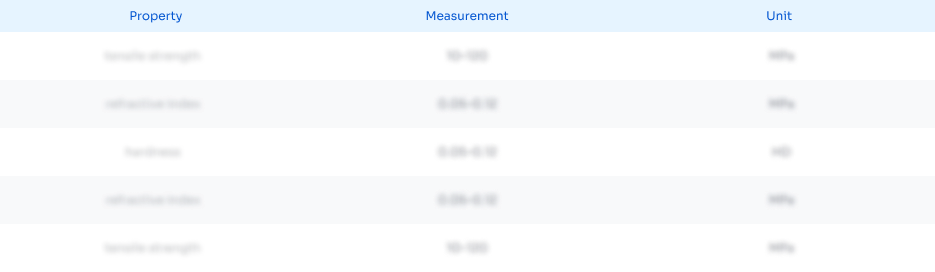
Abstract
Description
Claims
Application Information

- R&D Engineer
- R&D Manager
- IP Professional
- Industry Leading Data Capabilities
- Powerful AI technology
- Patent DNA Extraction
Browse by: Latest US Patents, China's latest patents, Technical Efficacy Thesaurus, Application Domain, Technology Topic, Popular Technical Reports.
© 2024 PatSnap. All rights reserved.Legal|Privacy policy|Modern Slavery Act Transparency Statement|Sitemap|About US| Contact US: help@patsnap.com