Friction stir welding stirring head
A friction stir welding and stirring head technology, applied in welding equipment, non-electric welding equipment, metal processing equipment, etc., can solve the problems of low welding quality and efficiency, poor heat dissipation, etc., to reduce heat concentration, improve welding quality and efficiency , good stability effect
- Summary
- Abstract
- Description
- Claims
- Application Information
AI Technical Summary
Problems solved by technology
Method used
Image
Examples
Embodiment Construction
[0021] In order to make the object, technical solution and advantages of the present invention clearer, the present invention will be further described in detail below in conjunction with the accompanying drawings and embodiments. It should be understood that the specific embodiments described here are only used to explain the present invention, not to limit the present invention.
[0022] see Figure 2-5 , The embodiment of the present invention provides a friction stir welding stirring head, which includes a clamping part 1 , a shoulder part 2 and a needle tip part 3 .
[0023] The clamping part 1 is used to install the stirring head, that is, to fix the stirring head on the clamping device, so as to realize the synchronous rotation of the stirring head and the clamping device. The shoulder part 2 is a transition part between the clamping part 1 and the needle tip part 3 , and is used for connecting the clamping part 1 and the needle tip part 3 . The needle point 3 is used...
PUM
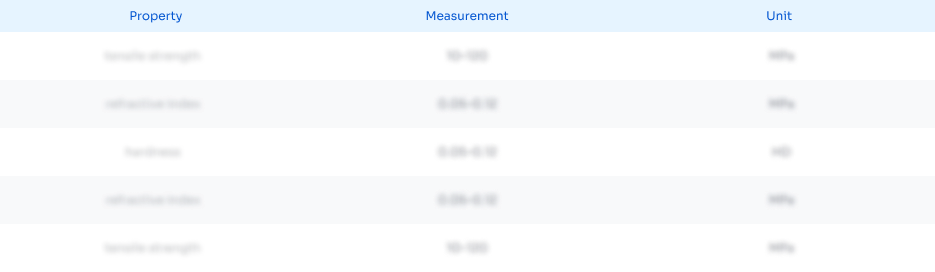
Abstract
Description
Claims
Application Information

- R&D Engineer
- R&D Manager
- IP Professional
- Industry Leading Data Capabilities
- Powerful AI technology
- Patent DNA Extraction
Browse by: Latest US Patents, China's latest patents, Technical Efficacy Thesaurus, Application Domain, Technology Topic, Popular Technical Reports.
© 2024 PatSnap. All rights reserved.Legal|Privacy policy|Modern Slavery Act Transparency Statement|Sitemap|About US| Contact US: help@patsnap.com