Preparation method of degradable rosin resin
A technology of rosin resin and rosin, which is applied in the direction of rosin adhesive, chemical modification of natural resin, plastic recycling, etc., to achieve the effect of good viscosity and good compatibility
- Summary
- Abstract
- Description
- Claims
- Application Information
AI Technical Summary
Problems solved by technology
Method used
Image
Examples
Embodiment 1
[0045] (1) 600 grams of masson rosin are dropped into a reaction flask equipped with a thermometer and agitator, heated to 180° C. for melting under nitrogen protection;
[0046] (2) Put in 15 grams of fumaric acid, and keep warm at 200°C for 1 hour after adding;
[0047] (3) Add 1.8 grams of mixed catalyst (a mixture of 4,4'-thiobis(6-tert-butyl-3-methylphenol) and zinc oxide at a mass ratio of 1.8:1), 48 grams of ethylene glycol, and 12 grams of glycerin 1. 6 grams of sorbitol, stirred and reacted at 220°C for 1 hour, then stirred and reacted at 250°C for 1 hour, and stirred and reacted at 275°C for 7 hours;
[0048] (4) Remove the water generated by the reaction in vacuum, cool to 220°C, add 0.9 grams of antioxidant 2,6-di-tert-butyl-4-methylphenol, degradation accelerator (potassium dihydrogen phosphate, iron stearate and 3 grams of cerium diethyldithiocarbamate according to the mass ratio of 3:5:1 mixture), stir evenly, and discharge to obtain rosin resin.
Embodiment 2
[0050] (1) 600 grams of masson rosin are dropped into a reaction flask equipped with a thermometer and agitator, heated to 180° C. for melting under nitrogen protection;
[0051](2) Add 3 grams of mixed catalyst (a mixture of 4,4'-thiobis(6-tert-butyl-3-methylphenol) and zinc oxide at a mass ratio of 1.8:1), 90 g of ethylene glycol, and 6 grams of glycerin 1. 3 grams of sorbitol, stirred and reacted at 200°C for 1 hour, then stirred and reacted at 225°C for 1 hour, and stirred and reacted at 250°C for 7 hours;
[0052] (4) Remove the water generated by the reaction in vacuum, cool down to 180°C, add 3 grams of antioxidant 2,6-di-tert-butyl-4-methylphenol, degradation accelerator (sodium dihydrogen phosphate, iron stearate and 6 grams of cerium diethyldithiocarbamate according to the mass ratio of 3:5:1 mixture), stir evenly, and discharge to obtain rosin resin.
Embodiment 3
[0054] (1) 600 grams of wetland rosin are dropped into a reaction flask equipped with a thermometer and a stirrer, heated to 180° C. for melting under nitrogen protection;
[0055] (2) drop in 48 grams of maleic anhydride, and keep warm at 160° C. for 1 hour after adding;
[0056] (3) Add 0.06 g of mixed catalyst (a mixture of 4,4'-thiobis(6-tert-butyl-3-methylphenol) and zinc oxide at a mass ratio of 1.8:1), 36 g of ethylene glycol, and 18 g of glycerin 12 grams of sorbitol, stirred and reacted at 250°C for 1 hour, then stirred and reacted at 275°C for 1 hour, and stirred and reacted at 290°C for 5 hours;
[0057] (4) Remove the water generated by the reaction in vacuum, cool to 240°C, add 0.06 g of antioxidant 2,6-di-tert-butyl-4-methylphenol, degradation accelerator (sodium dihydrogen phosphate, zinc stearate and 0.3 g of cerium diethyldithiocarbamate according to the mass ratio of 3:5:1 mixture), stir evenly, and discharge to obtain rosin resin.
PUM
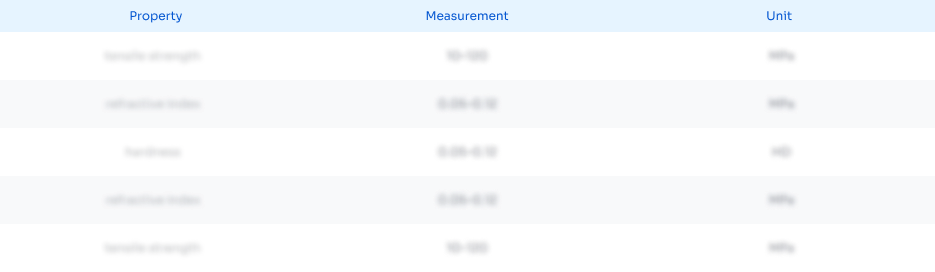
Abstract
Description
Claims
Application Information

- R&D Engineer
- R&D Manager
- IP Professional
- Industry Leading Data Capabilities
- Powerful AI technology
- Patent DNA Extraction
Browse by: Latest US Patents, China's latest patents, Technical Efficacy Thesaurus, Application Domain, Technology Topic, Popular Technical Reports.
© 2024 PatSnap. All rights reserved.Legal|Privacy policy|Modern Slavery Act Transparency Statement|Sitemap|About US| Contact US: help@patsnap.com