Water-based graphene heat dissipation coating as well as preparation and spraying methods thereof
A technology of water-based graphene and heat-dissipating coatings, which is applied in coatings and other directions, can solve the problems that graphene is difficult to form heat conduction paths, and the heat dissipation effect cannot meet the application requirements, so as to reduce interface scattering, excellent thermal conductivity, and improve heat conduction paths. effect of ability
- Summary
- Abstract
- Description
- Claims
- Application Information
AI Technical Summary
Problems solved by technology
Method used
Image
Examples
preparation example Construction
[0019] The second aspect of the present disclosure provides the preparation method of the water-based graphene heat-dissipating coating described in the first aspect, characterized in that, the method comprises the following steps: S1, mixing the water-based resin, deionized water and the first additive It is dispersed and stirred to obtain the first mixture; S2, adding heat-conducting particles, conductive carbon black and graphene dispersion slurry to the first mixture to obtain the second mixture; S3, grinding the second mixture into the solid The particle size of the material is less than 10 μm, and the thermally conductive black slurry is obtained by filtering; S4, adding the thermally conductive black slurry, deionized water, water-based resin and the second additive into the container and stirring evenly to obtain a water-based graphene heat-dissipating coating; the step S2 is also The method includes: adding grinding media to the second mixture, and the mass ratio of th...
Embodiment 1
[0026] (1) Mix 42g of water-based hydroxyl acrylic resin, 4.5g of deionized water, 9.2g of the first additive (1.2g of dispersant TNWDIS, 1.5g of dispersant Dego-755W, 1.5g of dispersant BYK190, 3.75g of dispersant 4900 and 1.25 g antifoaming agent Dego-902W) is mixed and added in the grinding jar, dispersed and stirred for 1h at a rotating speed of 800rpm to obtain a uniformly stirred first mixture; then add 88g graphene dispersion slurry, 5.25g carbon nanotubes in the first mixture , 1.05g conductive carbon black, and then add zirconia beads of 0.8~1.0mm and 1.4~1.6mm to obtain the second mixture. The mass ratio of zirconia beads is 2:1, and the zirconia beads in the second mixture are filtered and removed to obtain a thermally conductive black slurry; 92g of thermally conductive black slurry, 4.5g of deionized water, and 3.5g of the second auxiliary agent are weighed. Add the agent (0.5g coupling agent LD-9S, 1g defoamer BYK-028, 1g film forming agent dodecyl alcohol ester,...
Embodiment 2
[0035] (1) 42g water-based hydroxyacrylic resin, 4.5g deionized water, 9.2g first additives (1.2g wetting agent BYK349, 1.5g dispersant Dego-755W, 1.5g dispersant BYK190, 3.75g dispersant 4900 and 1.25g defoamer Dego-902W) was added into the grinding jar, dispersed and stirred for 1h at 800rpm to obtain a uniformly stirred mixture; then 88g graphene dispersion slurry, 5.25g rod-shaped zinc oxide, and 1.05g conductive carbon were added to the mixture Black, and then add zirconia beads of 0.8-1.0mm and 1.4-1.6mm to obtain the second mixture. The amount of zirconia beads added is 35% of the mass of the second mixture, and the mass ratio of zirconia beads of two particle sizes is 2 : 1, ground to a particle size of less than 10 μm, the zirconia beads in the second mixture are removed by filtration to obtain a thermally conductive black slurry; 92g of thermally conductive black slurry, 4.5g deionized water, 3.5g of the second auxiliary agent (0.5g Joint agent LD-9S, 1g defoamer BYK...
PUM
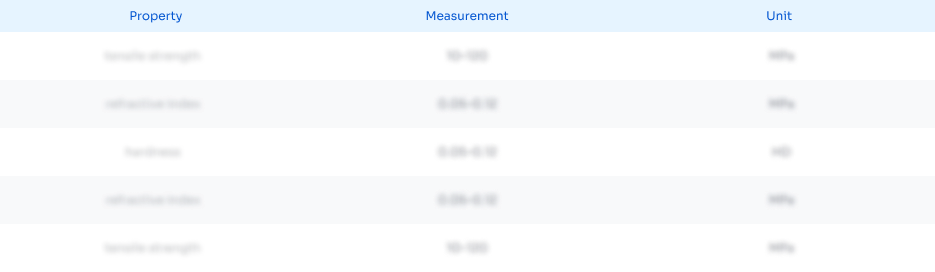
Abstract
Description
Claims
Application Information

- R&D Engineer
- R&D Manager
- IP Professional
- Industry Leading Data Capabilities
- Powerful AI technology
- Patent DNA Extraction
Browse by: Latest US Patents, China's latest patents, Technical Efficacy Thesaurus, Application Domain, Technology Topic, Popular Technical Reports.
© 2024 PatSnap. All rights reserved.Legal|Privacy policy|Modern Slavery Act Transparency Statement|Sitemap|About US| Contact US: help@patsnap.com