Forming technology of outdoor epoxy resin composite material product
An epoxy resin and composite material technology, which is applied in packaging/dipping, electrical components, inductor/transformer/magnet manufacturing, etc., can solve the problems of pulverization on the surface of the product, high requirements for paint adhesion, and poor paint weather resistance. Reliable waterproof and mechanical strength, reliable process and performance, and excellent weather resistance
- Summary
- Abstract
- Description
- Claims
- Application Information
AI Technical Summary
Problems solved by technology
Method used
Image
Examples
Embodiment 1
[0035] The invention provides a new molding process for outdoor electrical products. Taking the medium-voltage voltage transformer as an example, according to the shape of the required product, a mold (as an inner mold) slightly smaller than the shape is designed to carry out the molding process. In the S1 step, before the S1 step, the iron core and winding of the product components are prepared, and the iron core, winding and inner mold are preheated. The inner mold can be made of various heat-conducting materials with good heat resistance, reducing the Thermal deformation has an impact on the product and process. Step S1 is the installation of the inner module. Install the preheated iron core and windings required for insulation packaging in the inner mold as a semi-finished inner tank. After the inner mold is assembled, the curing molding step of the semi-finished product of the S2 inner tank is carried out, and the indoor epoxy resin composite material is used for vacuum ca...
Embodiment 2
[0037] The invention provides a new molding process of outdoor electrical products. Taking small outdoor insulating electrical appliances as an example, the inner mold and small outdoor insulating electrical accessories are pre-baked first, and the small outdoor insulating packages required for insulating packaging are installed in the inner mold. For electrical appliances, the inner mold is filled with epoxy resin composite material, vacuum poured, automatic pressure gel injection is performed, and then placed in an oven for curing and molding, and then the inner film is demoulded, the surface of the semi-finished product is cleaned, and the surface release agent is cleaned. Then apply a coupling agent on the surface of the semi-finished product. The coupling agent is to increase the adhesion between epoxy resin and silicone rubber and enhance product quality. Install the semi-finished outdoor epoxy resin composite material coated with the coupling agent in the outer mold. At t...
PUM
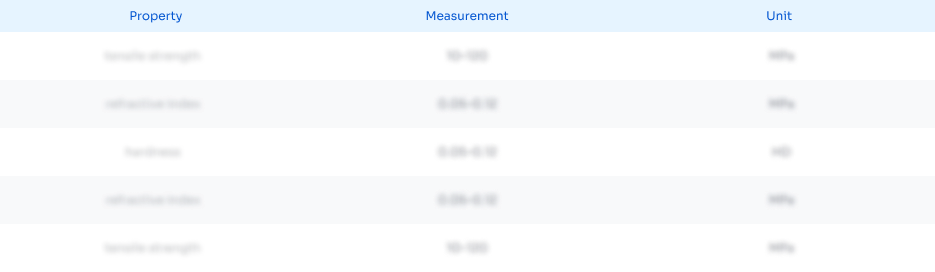
Abstract
Description
Claims
Application Information

- Generate Ideas
- Intellectual Property
- Life Sciences
- Materials
- Tech Scout
- Unparalleled Data Quality
- Higher Quality Content
- 60% Fewer Hallucinations
Browse by: Latest US Patents, China's latest patents, Technical Efficacy Thesaurus, Application Domain, Technology Topic, Popular Technical Reports.
© 2025 PatSnap. All rights reserved.Legal|Privacy policy|Modern Slavery Act Transparency Statement|Sitemap|About US| Contact US: help@patsnap.com