Robot frogman, shape memory alloy wire driving assembly and manufacturing method of shape memory alloy wire driving assembly
A memory alloy wire and drive component technology, applied in the field of robotics, can solve problems such as improving the sealing structure and cost, energy waste, and the inability to use the speed of seawater movement.
- Summary
- Abstract
- Description
- Claims
- Application Information
AI Technical Summary
Problems solved by technology
Method used
Image
Examples
Embodiment 1
[0035] see figure 1 , in this embodiment, the overall structure of the robot frogman is similar to the structure of the robot frogman disclosed in the patent literature of CN111152244A, and the specific structure is as follows figure 1 As shown, the robot frogman 1 specifically includes a fuselage 10 and a humanoid mechanical arm 11 installed on the fuselage 10, a humanoid mechanical leg 19 and a control unit. The humanoid robotic arm 11 includes a shoulder joint 12, a large arm 13. The elbow joint 14, the forearm 15 and the claw assembly 2 connected to the end of the forearm 15 through the wrist joint. During the working process, it communicates with the transfer station 02 on the water surface through the optical fiber 01.
[0036] In this embodiment, it is mainly to improve the shape-memory alloy wire driving mechanism on the palm assembly of the robot frogman disclosed in the patent document CN111152244A. The driving component structure of the shape memory alloy wire use...
Embodiment 2
[0052] As a description of Embodiment 2 of the present invention, only the differences from Embodiment 1 above will be described below. That is, in this embodiment, on the basis of using the shape memory alloy wire driving assembly in Embodiment 1, the structure of the driving mechanism is further improved.
[0053] like Figure 4 to Figure 7 As shown, the gripper assembly 2 includes a palm, a pick-and-place driver and a gripper 21 swingably mounted on the palm, wherein the number of grippers 21 is multiple, specifically three or two; The claws 21 are driven to swing back and forth between the grasping position and the release position, wherein, in the grasping position, the three curved claws 21 are synchronously driven and closed for grasping target objects such as fish; At the release position, the three curved claws 21 are synchronously driven to open to release the clamped target object. The control unit is used for controlling the action of the pick-and-place driver ac...
PUM
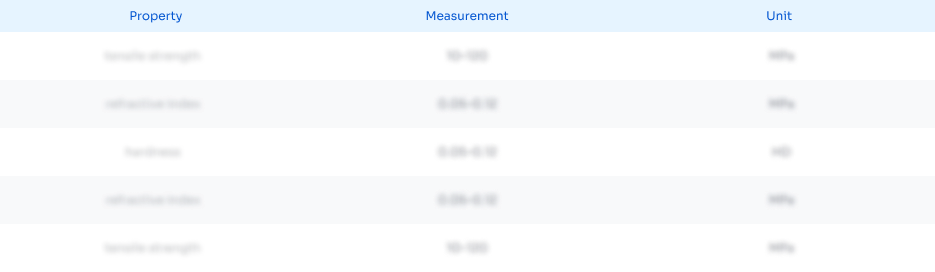
Abstract
Description
Claims
Application Information

- R&D Engineer
- R&D Manager
- IP Professional
- Industry Leading Data Capabilities
- Powerful AI technology
- Patent DNA Extraction
Browse by: Latest US Patents, China's latest patents, Technical Efficacy Thesaurus, Application Domain, Technology Topic, Popular Technical Reports.
© 2024 PatSnap. All rights reserved.Legal|Privacy policy|Modern Slavery Act Transparency Statement|Sitemap|About US| Contact US: help@patsnap.com