Industrial robot distributed control system middleware framework
A robot middleware and distributed control technology, applied in the general control system, control/regulation system, comprehensive factory control, etc., can solve problems such as inability to adjust resource allocation, difficult to achieve optimal system performance, and high coupling degree
- Summary
- Abstract
- Description
- Claims
- Application Information
AI Technical Summary
Problems solved by technology
Method used
Image
Examples
Embodiment Construction
[0022] The present invention will be further described in detail below in conjunction with the accompanying drawings and specific embodiments.
[0023] The purpose of the present invention is to learn from the mature industrial distributed control system (DCS) concept, combined with the SOA architecture, and to meet the workshop-level or plant-level production control requirements of industrial robots in complex industrial production environments, and propose an open distributed industrial robot. Control System (RDCS) middleware framework. Based on the RDCS middleware architecture, the present invention uses the distributed node control station as the middleware container, and the application developer of the industrial robot business scene calls the component development and application through the node control station, so that the development of the industrial robot application program is compatible with the robot hardware and The operating system platform is independent, sh...
PUM
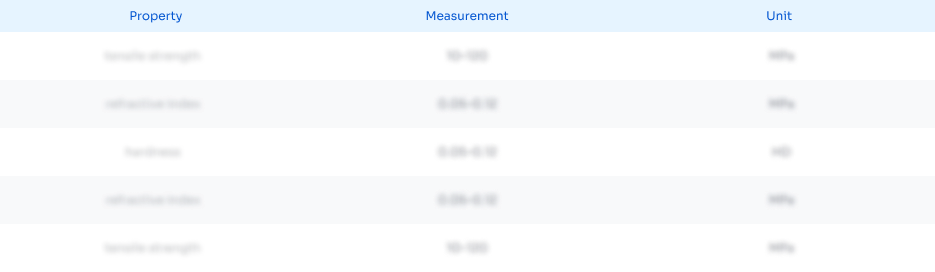
Abstract
Description
Claims
Application Information

- R&D
- Intellectual Property
- Life Sciences
- Materials
- Tech Scout
- Unparalleled Data Quality
- Higher Quality Content
- 60% Fewer Hallucinations
Browse by: Latest US Patents, China's latest patents, Technical Efficacy Thesaurus, Application Domain, Technology Topic, Popular Technical Reports.
© 2025 PatSnap. All rights reserved.Legal|Privacy policy|Modern Slavery Act Transparency Statement|Sitemap|About US| Contact US: help@patsnap.com