Preparation process of light foam concrete with high compressive property
A technology of lightweight foam and compressive performance, applied in the field of building materials, can solve the problems of affecting the strength of foam lightweight soil, poor utilization of building materials, and increase the water absorption rate of the matrix, so as to improve the reasonable utilization rate, increase environmental protection, avoid effects of excess moisture
- Summary
- Abstract
- Description
- Claims
- Application Information
AI Technical Summary
Problems solved by technology
Method used
Image
Examples
Embodiment 1
[0028] Such as Figure 1-3 As shown, the present invention provides a process for preparing lightweight foamed concrete with high compressive performance. The lightweight foamed concrete with high compressive performance is made of composite concrete and foaming agent, and also includes the following steps:
[0029] Step 1. Prepare composite concrete: first add water to the mixer of the hydraulic foaming machine, then put cement, fly ash, gypsum, water reducing agent and concrete reinforcing agent into the mixer and stir for 0.5 to 2 minutes.
[0030] Step 2, preparing the foaming agent aqueous solution: mixing and stirring the foaming agent foam and water at a weight percentage of 1:25-1:40, thereby preparing the foaming agent aqueous solution.
[0031] Step 3. Preparation of polystyrene foam: adding polystyrene resin to foaming agent, and simultaneously softening with internal heating of the mixer to generate gas to form a polystyrene foam with a rigid closed-cell structure....
Embodiment 2
[0035] Such as Figure 1-3 As shown, on the basis of Example 1, the present invention provides a technical solution: preferably, in the step of preparing composite concrete, the mass proportion of cement is 10% to 15%, and the mass proportion of fly ash is 20% to 15%. 30%, the mass proportion of water is 25% to 40%, the mass proportion of gypsum is 15% to 20%, the mass proportion of water reducing agent is 10% to 15%, and the mass proportion of concrete reinforcement is 5% to 15%. %, first mix cement and fly ash according to a certain ratio, then mix with gypsum and water reducer when mixing, and then add water according to the actual ratio to adjust the dilution.
[0036] In this embodiment, by mixing cement and fly ash according to a certain ratio in the step of preparing composite concrete, and then adding gypsum, water reducing agent, and concrete reinforcing agent, the strength of the material is used to increase the strength during the preparation of composite concrete. ...
Embodiment 3
[0038] Such as Figure 1-3 As shown, on the basis of Example 1, the present invention provides a technical solution: preferably, in the preparation of polystyrene foam, the mass proportion of polystyrene resin is 10% to 30%, and the mass proportion of foaming agent is 20% to 35%, in the preparation of polystyrene foam, when the polystyrene resin is added to the foaming agent and mixed with the mixer and heated, cooperate with the heating net installed on the inner wall of the mixer, so that when the polystyrene resin and the foaming agent are stirred and mixed, they can be uniform Heating to prepare lightweight foamed concrete, the mass proportion of composite concrete is 40% to 45%, the mass proportion of polystyrene foam is 40% to 45%, and the mass proportion of foaming agent aqueous solution is 5% to 10%, followed by Enter the mixer, stir and mix to prepare light foam concrete, put the foaming agent aqueous solution into the mixer, use the function of heating and stirring t...
PUM
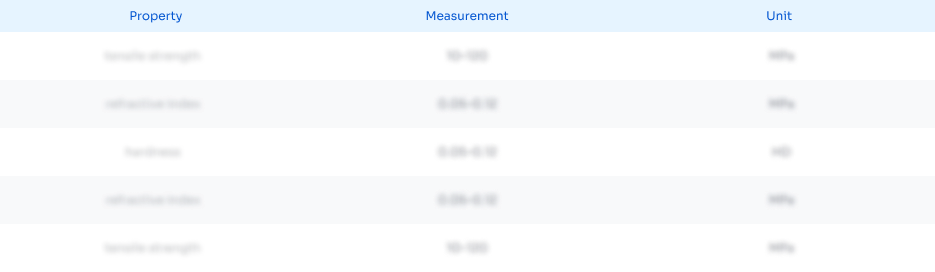
Abstract
Description
Claims
Application Information

- R&D
- Intellectual Property
- Life Sciences
- Materials
- Tech Scout
- Unparalleled Data Quality
- Higher Quality Content
- 60% Fewer Hallucinations
Browse by: Latest US Patents, China's latest patents, Technical Efficacy Thesaurus, Application Domain, Technology Topic, Popular Technical Reports.
© 2025 PatSnap. All rights reserved.Legal|Privacy policy|Modern Slavery Act Transparency Statement|Sitemap|About US| Contact US: help@patsnap.com