White-core malleable cast iron decarburization process
A cast iron and decarburization technology, applied in the field of cast iron decarburization technology, can solve the problem of high scrap rate of cast iron, achieve the effects of improving quality, avoiding extremely high hardness of sintered material, and reducing scrap and waste
- Summary
- Abstract
- Description
- Claims
- Application Information
AI Technical Summary
Problems solved by technology
Method used
Image
Examples
Embodiment 1
[0062] A white heart malleable iron decarburization process, comprising the following steps
[0063] S1. Prepare raw materials
[0064]Castings, its components include by weight: 13.8 parts of steel scrap, 0.4 parts of recarburizer and 21 parts of returned materials; Iron oxide scale 2-2.5 parts;
[0065] S2. Raw materials enter the furnace
[0066] Put the casting into the heat treatment furnace, add a decarburizer to mix the materials; seal the heat treatment furnace after the materials are mixed;
[0067] S3. Heat treatment
[0068] Heating process: heat up the mixed materials in the heat treatment furnace in sequence, the heating time is 20h, the temperature after heating is 1050°C, and the heating rate is 50°C / h;
[0069] Heat preservation process: maintain the temperature after heating for 70h;
[0070] Cooling process: (1) The first stage of cooling: the temperature is lowered to 780 degrees Celsius at a cooling rate of 30°C / h, that is, the cooling time is 9h; (2) ...
Embodiment 2
[0087] The exothermic decarburizer is added to each part of the casting, including 1.3 parts by weight of iron oxide scale and 1.3 parts of iron ore; the rest are the same as in Example 1.
[0088] The decarburized castings are tested, and the carbon content in the interval 0-1mm from the outer surface is 0.07%, and the carbon content in the interval 2-2.5mm is 0.56%;
Embodiment 3
[0090] A white heart malleable iron decarburization process, comprising the following steps
[0091] S1. Prepare raw materials
[0092] Castings include: 13.8 parts of steel scrap, 0.4 parts of recarburizer and 21 parts of returned materials in parts by weight;
[0093] S2. Raw materials enter the furnace
[0094] Put the casting into the heat treatment furnace, add a decarburizer to mix the materials; seal the heat treatment furnace after the materials are mixed; add exothermic decarburizer to each part of the casting, including 0.5 parts by weight of iron oxide scale, iron ore 0.75 copies;
[0095] S3. Heat treatment
[0096] Heating process: heat up the mixed materials in the heat treatment furnace sequentially, the heating time is 5h, the temperature after heating is 1050°C, and the heating rate is 210°C / h;
[0097] (1) The first stage of heat preservation: maintain a high temperature of 1050 ° C for 80 hours;
[0098] (2) The second stage of heat preservation: suddenly...
PUM
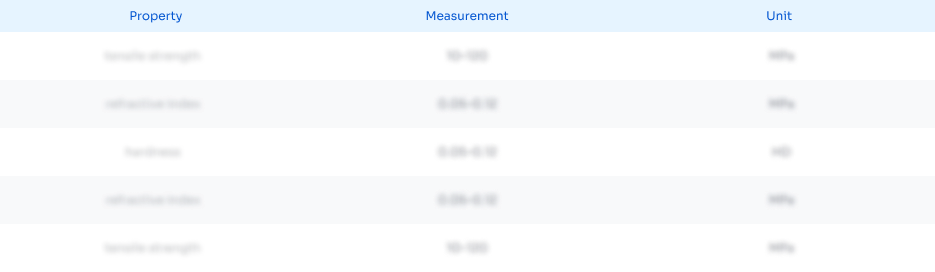
Abstract
Description
Claims
Application Information

- Generate Ideas
- Intellectual Property
- Life Sciences
- Materials
- Tech Scout
- Unparalleled Data Quality
- Higher Quality Content
- 60% Fewer Hallucinations
Browse by: Latest US Patents, China's latest patents, Technical Efficacy Thesaurus, Application Domain, Technology Topic, Popular Technical Reports.
© 2025 PatSnap. All rights reserved.Legal|Privacy policy|Modern Slavery Act Transparency Statement|Sitemap|About US| Contact US: help@patsnap.com