Shell highlight machining process and device thereof
A processing technology and processing device technology, applied in the field of shell mirror high-gloss processing technology and its device, can solve problems such as appearance influence, and achieve the effects of improving surface finish, low processing cost, and high versatility
- Summary
- Abstract
- Description
- Claims
- Application Information
AI Technical Summary
Problems solved by technology
Method used
Image
Examples
Embodiment Construction
[0042] The specific implementation manner of the present invention will be described in detail below in conjunction with the accompanying drawings.
[0043] The specific technical scheme is as follows:
[0044] Such as figure 1 As shown, on the one hand, the present invention provides a shell highlight processing technology, comprising the following steps:
[0045] (1) Carry out anodic oxidation for the first time on the shell surface;
[0046] (2) Determine the parameters of the high light treatment, and carry out high light treatment on the shell surface after the first anodic oxidation;
[0047] (3) Carrying out the second anodic oxidation on the surface of the shell after high light treatment;
[0048] (4) immersing the shell after the second anodic oxidation in the dye solution for dyeing treatment;
[0049] (5) Sealing the dyed shell.
[0050] Among them, the first anodic oxidation provided by the present invention does not carry out dyeing and sealing treatment, wh...
PUM
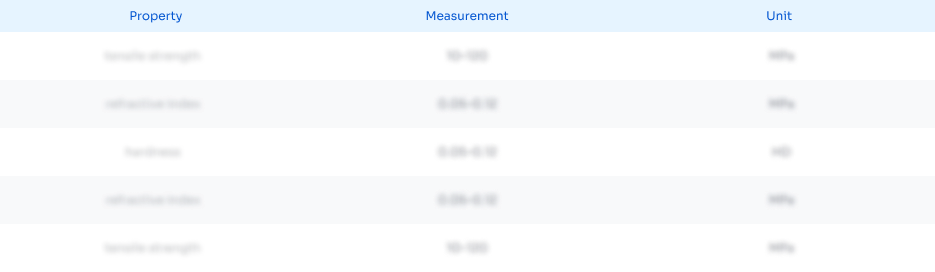
Abstract
Description
Claims
Application Information

- R&D Engineer
- R&D Manager
- IP Professional
- Industry Leading Data Capabilities
- Powerful AI technology
- Patent DNA Extraction
Browse by: Latest US Patents, China's latest patents, Technical Efficacy Thesaurus, Application Domain, Technology Topic, Popular Technical Reports.
© 2024 PatSnap. All rights reserved.Legal|Privacy policy|Modern Slavery Act Transparency Statement|Sitemap|About US| Contact US: help@patsnap.com