Automatic forging production line and process method for aero-engine bearing ring
A technology for aero-engines and bearing rings, applied in the direction of engine components, forging furnaces, manufacturing tools, etc., can solve the problems of uncontrollable punching forming force, unstable rolling speed, unstable forging speed, etc., and achieve stable Sex and consistency, avoiding the influence of human factors, and the effect of controllable punching force
- Summary
- Abstract
- Description
- Claims
- Application Information
AI Technical Summary
Problems solved by technology
Method used
Image
Examples
Embodiment Construction
[0026] The present invention will be further described in detail below in conjunction with the accompanying drawings and specific embodiments.
[0027] like figure 1 As shown, an automatic forging production line of an aero-engine bearing ring includes a first feeder 1, a second feeder 2, a first robot 3, a second robot 4, a third robot 5, a fourth robot 6, a first Five robots 7, medium-temperature heating furnace 8, first high-temperature heating furnace 9, second high-temperature heating furnace 10, three-station servo hydraulic press 11, transfer stage 12, first CNC automatic ring rolling machine 13, second CNC automatic rolling machine Ring machine 14 and discharge roller table 15; the first feeder 1 and the second feeder 2 are arranged side by side to form a material transfer unit, the material transfer unit, the first robot 3, the second robot 4, the fourth robot The robot 6, the transfer stage 12, the fifth robot 7, and the discharge roller table 15 are sequentially di...
PUM
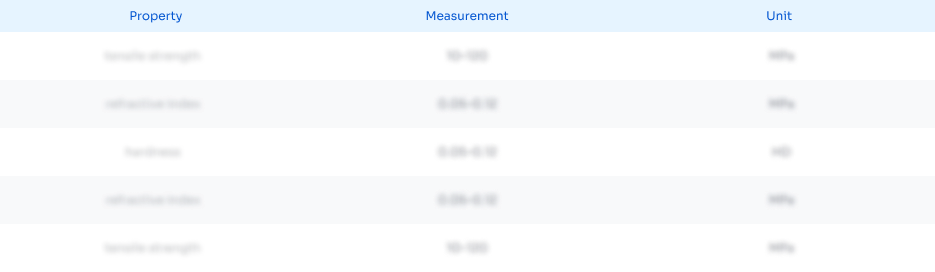
Abstract
Description
Claims
Application Information

- R&D Engineer
- R&D Manager
- IP Professional
- Industry Leading Data Capabilities
- Powerful AI technology
- Patent DNA Extraction
Browse by: Latest US Patents, China's latest patents, Technical Efficacy Thesaurus, Application Domain, Technology Topic, Popular Technical Reports.
© 2024 PatSnap. All rights reserved.Legal|Privacy policy|Modern Slavery Act Transparency Statement|Sitemap|About US| Contact US: help@patsnap.com