Rotor assembly of linear displacement sensor and linear displacement sensor
A linear displacement sensor and mover technology, applied in the field of sensors, can solve problems such as inability to install or difficult installation, single operation mode, narrow installation application range, etc., and achieve the effects of improving service life, increasing reliability, and improving mechanical properties
- Summary
- Abstract
- Description
- Claims
- Application Information
AI Technical Summary
Problems solved by technology
Method used
Image
Examples
Embodiment Construction
[0050] The present invention will be described in further detail and complete below in conjunction with specific embodiments. The following description is merely exemplary in nature and not intended to limit the disclosure, application or use.
[0051]Taking the linear differential transformer displacement sensor as an example, the principle of the linear differential transformer is briefly explained. The linear differential transformer displacement sensor is an inductive sensor that converts non-electrical mechanical displacement changes into proportional electrical parameter changes. When ignoring the coil parasitic capacitance and core loss, the equivalent circuit of the linear displacement sensor Figure 4 shown.
[0052] in Figure 4 middle: e 1 is the excitation voltage of the primary coil; L 1 , R 1 are the primary coil inductance and resistance respectively; L 21 , L 22 are the inductances of the two secondary coils; M 1 , M 2 Respectively, the primary and two...
PUM
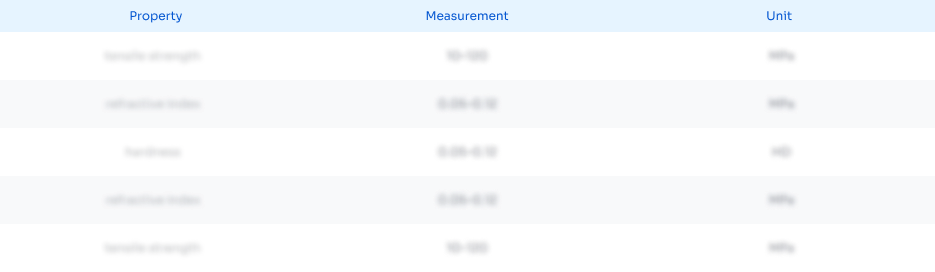
Abstract
Description
Claims
Application Information

- R&D Engineer
- R&D Manager
- IP Professional
- Industry Leading Data Capabilities
- Powerful AI technology
- Patent DNA Extraction
Browse by: Latest US Patents, China's latest patents, Technical Efficacy Thesaurus, Application Domain, Technology Topic, Popular Technical Reports.
© 2024 PatSnap. All rights reserved.Legal|Privacy policy|Modern Slavery Act Transparency Statement|Sitemap|About US| Contact US: help@patsnap.com